Thermax group
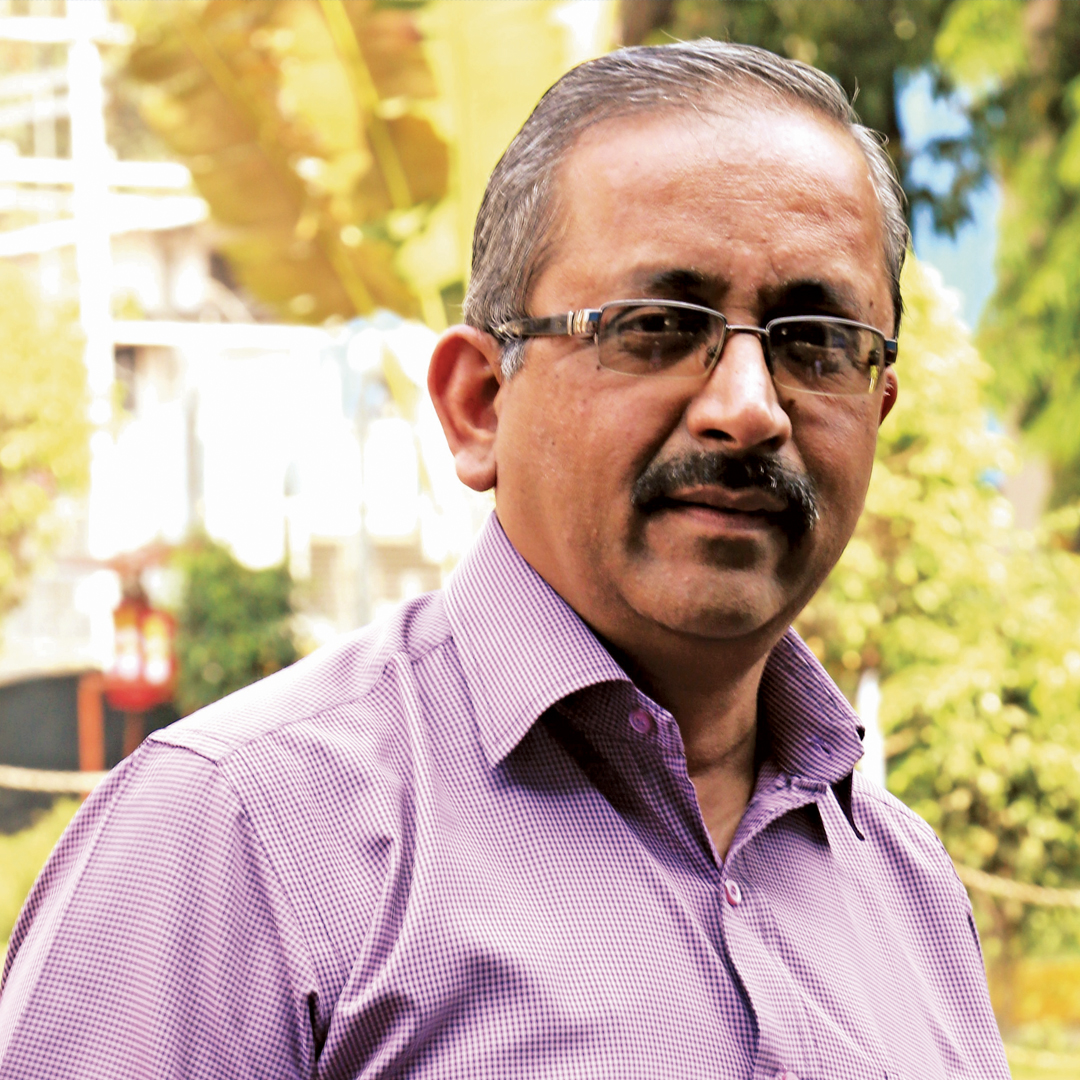
In 2016, as part of its ongoing efforts to achieve manufacturing excellence and step up productivity, Thermax unveiled a special initiative, Parivartan, at its facility in Savli, Gujarat. This improvement project was aimed to achieve stringent norms essential for the clients the company supports in global markets and make it a world-class manufacturing facility. The initiative was jointly driven with the CII. It began with the 5S methodology of lean manufacturing to organise the work place efficiently with a culture of discipline. It brought in employee involvement for participative contribution in improvements. The initiative resulted in identification and elimination of waste, which is continued as an ongoing process. Benefits from the programme included 10% space saving and significant energy savings.
At its older plant in Chinchwad too, Thermax focused on continuous improvement of the manufacturing processes, waste elimination and cost reduction. Over three hundred projects were completed with substantial cost reduction and cycle time reduction. Thermax also worked with supply chain partners for quality and delivery performance improvement which aided the manufacturing cycle time reduction.
Based on the capacities available at the company’s various manufacturing facilities and its chosen vendors, and depending on varying customer demand, Thermax is geared up for quick ‘make or buy’ decisions and maximise its capacity utilisation.
Two factors support this process of flexibility in manufacturing. First, the company-wide cost reduction drive helps in sourcing of manufacturing within own facility. Secondly, the company’s strategic and annual business planning helps forecast the available capacities and flexible decision making.