Anand Automotive (Gabriel)
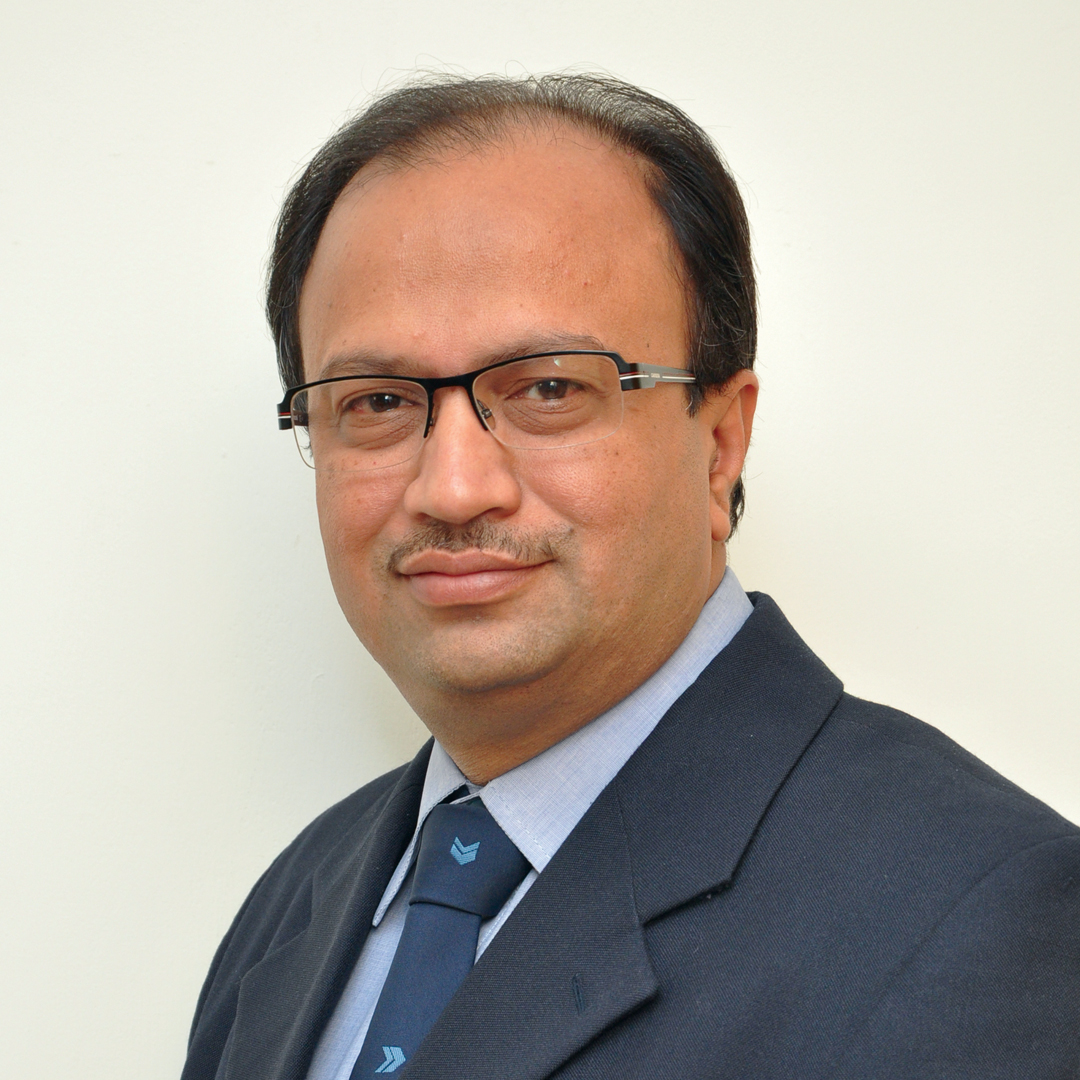
Gabriel has taken multiple initiatives to make its supply chain agile, flexible and benchmarked practices in Tier-1 segment. It took up the following steps last year: Heijunka Flow Integrated with SAP – Heijunka is a Japanese word, which mean (levelled production). The main tool kit for this project is taken from Toyota Production System. It has implemented this project at its Chakan plant, and will take it up with other Gabriel plants. There are three flows developed under Heijunka viz. procurement flow, production flow & delivery flow. All flows are linked to consumption of material which triggers to supplier schedule as well as in-house production planning. This process is fully automated without any manual intervention.
What it does is offer a system generated daily delivery request (DDR) to all vendor partners, ensures production flow that includes level production, mapping of safety stock across production lines, cell production capacity, line sequencing, availability of machines and resources. It is also looking at enterprise risk management to assess risk exposure pertaining to supply chain and strategy. For increasing engagement with suppliers, it has deployed real time information flow between each plants and respective vendors through vendor portal, and, recently, conducted Vendor satisfaction Survey through a third-party focusing on supplier relationship management.
The automotive industry is the only one of its kind that sees frequent product launches and new variants of existing models thus leading to overall reduction in product lifecycle. This throws multiple challenges in terms of handling higher variety of products with smaller lots sizes. Gabriel has taken the following steps: Production levelling during scheduling, defined static & dynamic safety stock, automation in transaction, and VSME programme.