Eaton
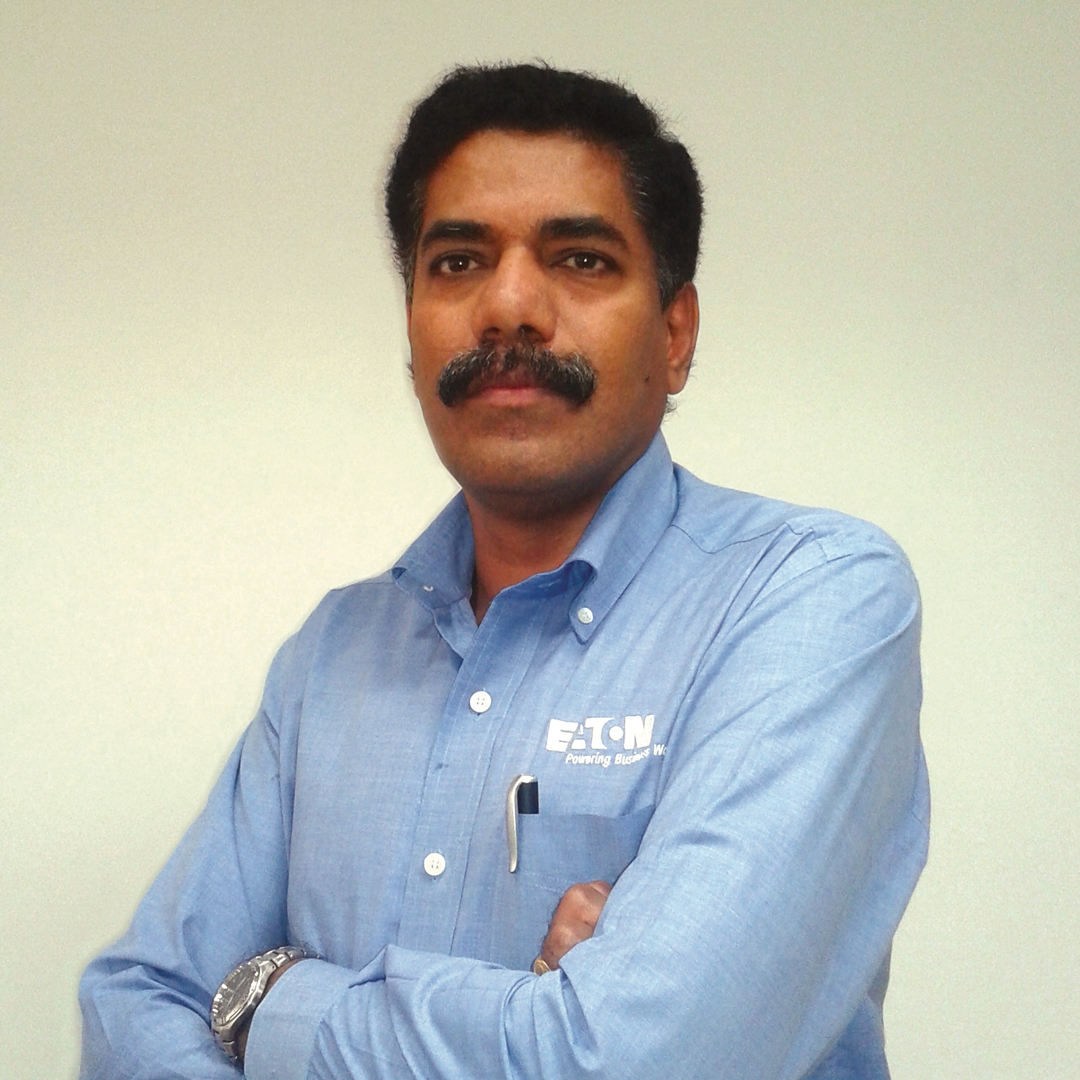
Eaton’s state-of-the-art vehicle transmission plant, at Ranjangaon, focused on improving safety, quality, manufacturing efficiency and sustainable practices in 2016. For instance, one of the initiatives looked at optimising processes that resulted in avoidance of capital investments, saving floor space and manpower reduction, and a 77% reduction in set-up time for critical machines. The initiative also substantially reduced energy consumption – lowering green house gases emissions (GHGE) by 4% i.e. equivalent to 82MT of CO2.
The Ranjangaon plant has also built a robust safety culture and this is evident from the fact that the plant has crossed 2,400+ days (in January 2017) without any recordable incidents. The National Safety Council (Maharashtra Chapter) has recognised the plant with awards for ‘longest accident free period’ and ‘lowest accident frequency rate’, consecutively in 2015 and 2016.
“Eaton is an integrated operating company and the Eaton Business System (EBS) is an embodiment of this philosophy. EBS allows us to implement and follow standard processes at all locations worldwide, transfer best practices and key learnings across the organisation and encourage a culture of continuous improvement,” offers Varadharajan.
In addition, their Continuous Improvement Framework, a management system that fosters the unique synthesis of standardisation and employee engagement in problem solving to create a fast learning and adaptive culture, helps them to stay flexible and address challenging business conditions.