Whirlpool Corporation
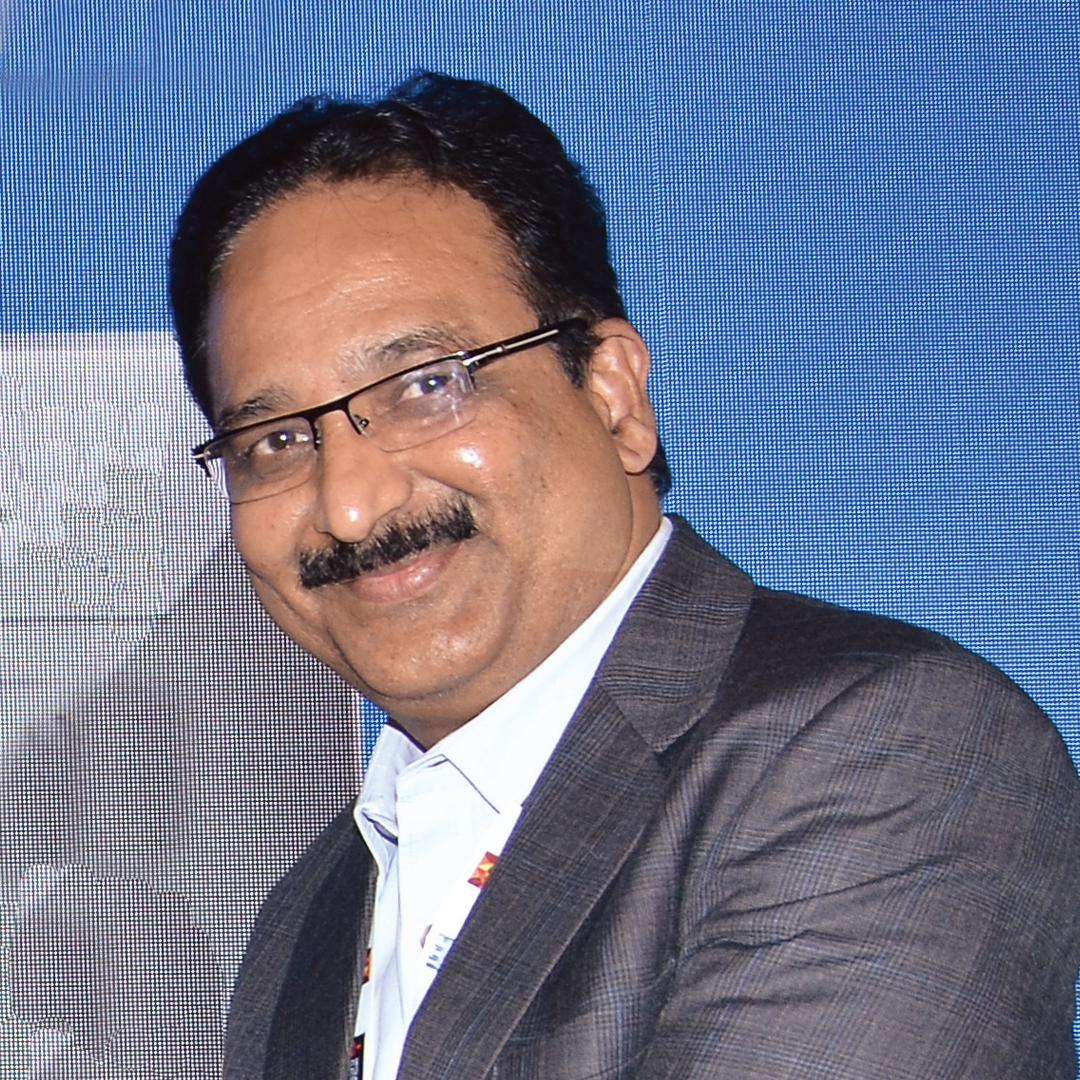
Last year, Whirlpool Corporation made significant improvements and achieved operational efficiency. It increased its per shift production that resulted in OEE improvement, and capacity enhancement of bottleneck M/Cs. it also reduced the head count by reducing NVA and line balancing error.
In terms of people engagement, it prefers to focus on experiences, behaviour and beliefs and used application of Training within Industry (TWI) for job instructions training to operators, and also integrated targets deployment to all levels. The Whirlpool Production System (based on lean philosophy) focused on visual management, standard work and daily PDCA and quality at source. It roped in management review cadence based on PDCA approach, that directs the management review to support, guide and accelerate results. The above steps resulted in an increase of 10% per shift production; a reduction in assembly line headcount to 75 (out of 650); about 20% improvement in people productivity; a little more than 10% improvement in quality defects; 4% net in manufacturing cost Improvement; and 99% people engagement score.
For 2017, the company is looking at production cycles flexibility through infrastructure flexibility, which means Industry 4.0 application in automation, advanced testing, data visibility and analytics, and agile manufacturing.
In terms of people flexibility, it wants to multi-skill production processes, and multi-skill for different operating formats.
Change Management would involve a structured programme on change management communication.