Power List 2020 – JLR
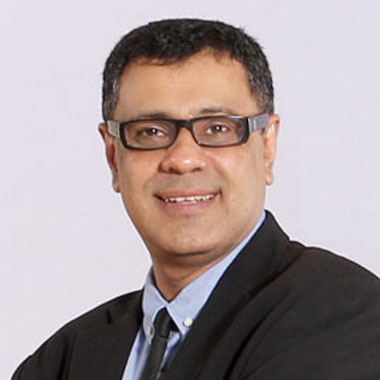
The Jaguar Land Rover Group was formed when India’s Tata Motors bought out Jaguar and Land Rover (Jaguar Land Rover) in 2008. Since then it has
become a global success story with products in demand around the globe.
Most of Jaguar Land Rover’s AM activities take place at the new Additive Manufacturing Centre, which is located within the Jaguar Land Rover Gaydon Centre, in Warwickshire, England. It houses a design, research and development centre, extensive test track facilities and is used
for the design and development of Jaguar and Land Rover vehicles.
This focus on sustainability is part of Jaguar Land Rover’s Destination Zero mission, which also looks at AM as a way to optimise both production processes and parts. From the development of 3D printed ergonomic gloves and sensory steering wheels to upcycling domestic waste to create high-quality materials for its vehicles, the Destination Zero mission is intended as a means to make societies safer, healthier and the environment cleaner.
For years, both Jaguar and Land Rover had been printing 3D parts for prototype use only. Recently that has changed, with a new generation of 3D printing technologies improving quality and lowering parts costs. Jaguar Land Rover secured early access to many of these additive manufacturing technologies,
including becoming the first in the UK to use HP’s multijet fusion process. The Jaguar XE SV Project 8 is one of the first vehicles to feature 3D printed
parts. The exclusive super saloon features multiple parts from Jaguar Land Rover’s Additive Manufacturing Centre, including brackets and interior trim.