Leading Manufacturing Companies – India Yamaha Motor
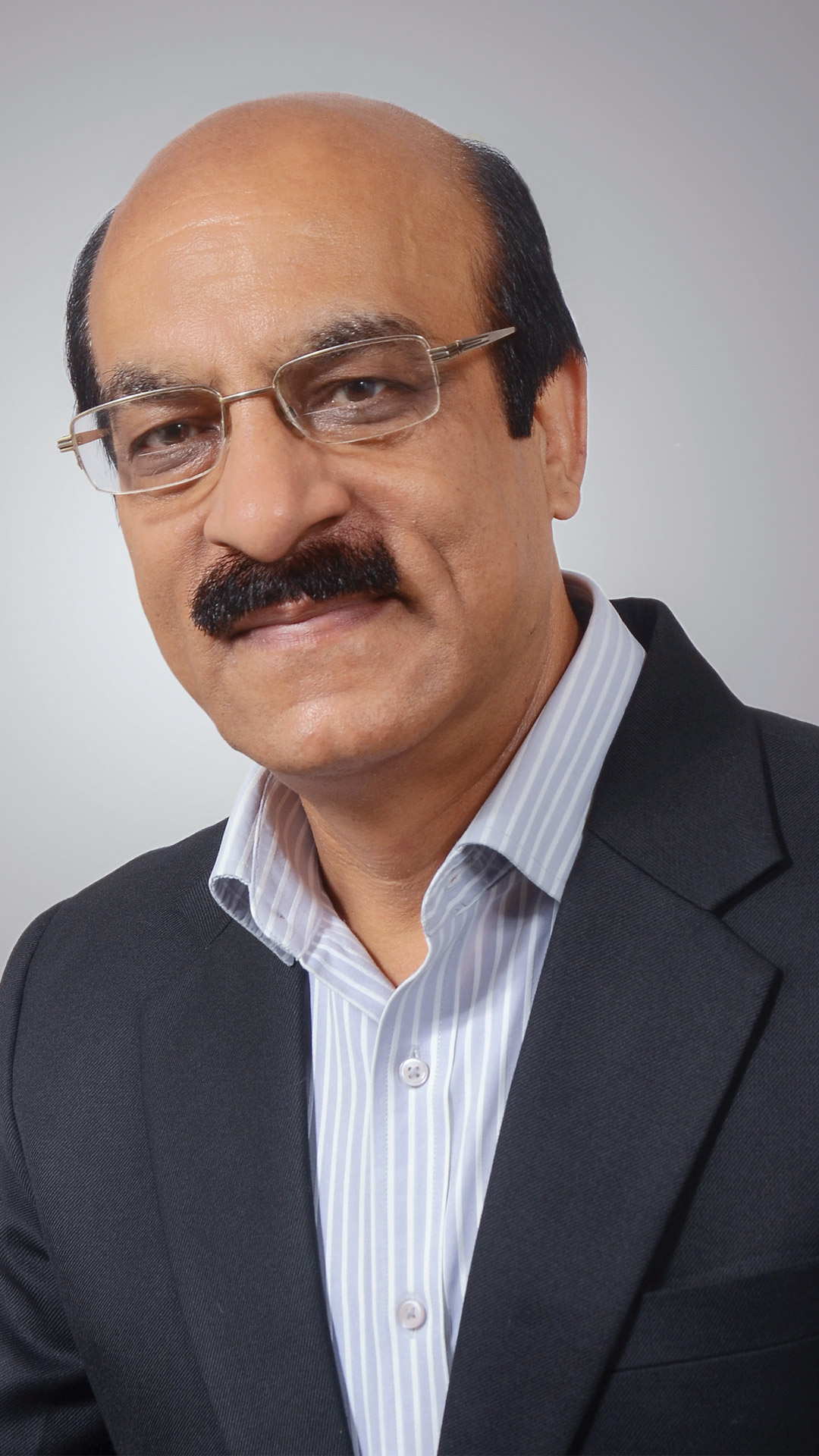
Product quality starts at the drawing stage. Whether it is the ease of manufacturing or usage of raw material, all parameters play a role in defining product quality. A standard procedure for robust process design consistently produces good quality products. Called Zenshu Ryohin, it has 7 steps that focus on design verification, defect-free process condition, quality process design setting & defect-free process management. The 7 steps have been set up systematically to ensure product quality — sustained and improved at each development stage. Even at the commercial stage, modifications and improvements are made to the manufacturing line to make high quality products as efficiently as possible.
Continuous improvement is challenged by striving to achieve global leadership by benchmarking quality indices to global standards. This is done by analysing global best practices and challenging creation of new benchmarks amongst Yamaha factories. Another method employed is Hyoujun Soubi activity. This focuses on creating standardised working methods to create a strong shop floor which resists changes and can improve continuously. From a traditional batch-production system, they have evolved to Just In Time. Sub-assemblies are set up next to the main assembly lines, and cycle times of processes have been synchronised to ensure required stock.
There is strong focus on training resources. A considerable amount of time is spent on training resources to ensure a ready pool of trained manpower for each processes. The main driving motto is “Customer No.1”, so all strategies are aligned to this one goal.