Top 50 Companies 2019 – vecv
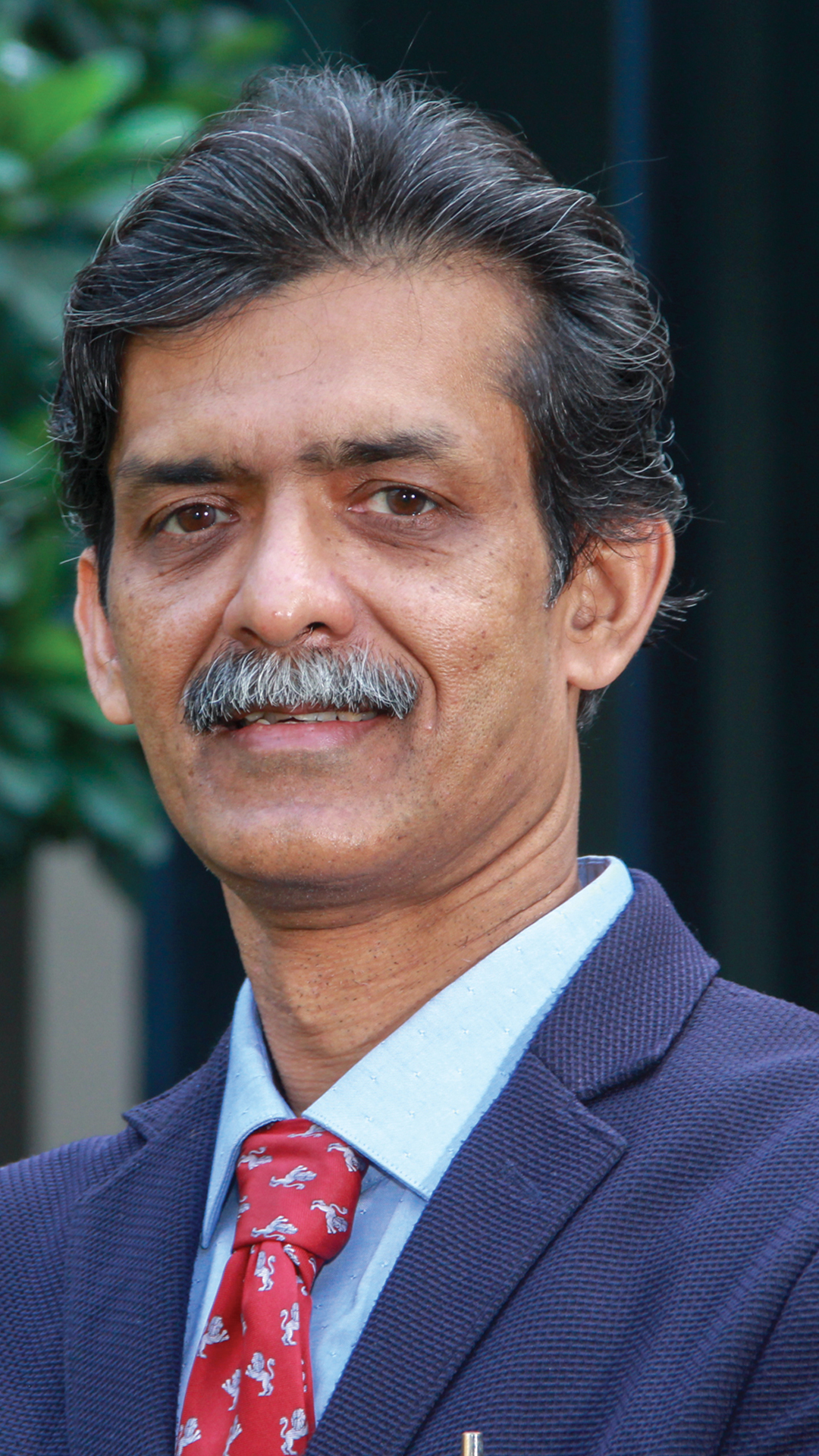
VECV is experimenting using VR devices connected to its PLM software. “This is powerful digital manufacturing tool allowing us to virtually define, plan, create, monitor and control production processes. It is used from early process planning and assembly simulation to a complete definition of the production facility and equipment. It results in crashing the lead time to market for new products,” says Srivastava.
The VR device working in conjunction with its Manufacturing Execution System (MES) and helps in deskilling complex operations on the assembly line. MES ensures error proofing and right parts selection. The history of each operation performed on vehicles can also be traced.
To enhance supply chain efficiency, the company has installed pick to light and kitting system on the shop floor. The existing truck capacity has reached to produce 90k trucks per annum which is global benchmark in terms of more than 1,000 vehicles production per acre of land. Relentless efforts put in by the operations team ensures best asset utilisation in terms of infrastructure.
Srivastava says in the present scenario, the major challenge for manufacturing is to improve productivity and controlling cost in a dynamic and fluctuating market. Market expansion and customer expectations pose challenges to ensure best quality product in minimum lead time. Also manufacturing industry is going through a major transformation for adopting rapid advancements in technologies.
VECV is increasingly adopting and leveraging IoT. Linked to its ERP systems, the IoT based MES helps them remain competitive and deliver more value to customers.
There’s also a focus on deskilling of manpower through Skill Dozo Centre and development of soft tool for optimisation of production planning & control. Going forward, VECV plans to reach world class quality with a vision for zero irritant, zero rust and zero rework. The team has started Mission 20-20 to achieve world class quality. Emphasis will be on structured QRQC, process standardisation, defect detection system (DDS), quality matrix, PFMEA, and MEx (digitisation) deployment. Team will adopt best practices using Volvo Production System (VPS).