Many industries have opted for automation to achieve efficient production and manage increased labour costs. The term “industrial automation” refers to much more than just robotics; it categorizes both software and hardware and serves as a mechanism which combines them. As a result of the exponential growth in the automation industry in recent years, numerous industries have shifted to automation. Businesses and SMEs which weren’t previously leveraging Industrial automation are adopting this trend rapidly.
The role of automation in Industry 4.0
We are in the midst of an advanced industrial revolution that allows complex machinery and processes to be managed much more effectively and affordably than ever before. By reducing the need for human labour in redundant and dangerous processes, automation allows businesses to focus on critical operations, energy usage, and safety. Because of the numerous technological changes that are affecting our industries, there is an urgent need for high-end, precise products that can only be met by high levels of productivity. Engineering systems, automated manufacturing, and industrial automation all play a role here.
Industry 4.0 and automation are currently taking shape thanks to technologies such as AI, 5G, advanced automation, advanced sensing, and many others. These have significantly altered how various industries operate and their processes are carried out. Automation in Industry 4.0 emphasises efficiency and optimization while significantly reducing the possibilities for errors. In a manual process where the margin of error can reach up to 10% when humans carry out the work, an automated platform can reduce it up to 0.00001%.
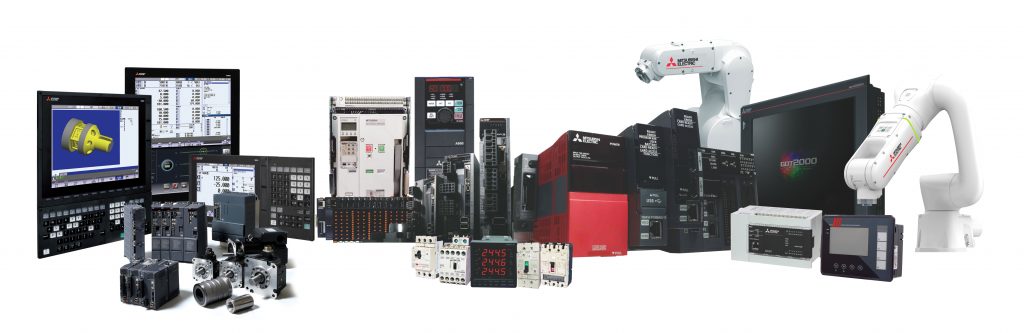
The advantages of industrial automation
In addition to discrete manufacturing firms, the following factors are propelling new market entrants into the industrial automation sector:
• Cost-efficiency: Since, automation requires less human intervention, it reduces production costs. Aside from that, virtual and augmented reality helps to increase productivity in business models and facilitate learning.
• Competitive advantages: Due to the nature of industrial automation technology, production is continuous and operational 24*7. As a result, it provides competitive advantages in terms of increased productivity, capacity, and process quality while minimising task errors and the cost of downtime.
• Time reduction: The time for information processing is reduced due to Automation 4.0. The platform has a sizable capacity for storing and managing data generated by processes.
• Flexibility and scalability: A human operator needs training because the industrial sector is dynamic and the tasks constantly change. The flexibility and scalability of robots and machines are maintained because they can be tightly programmed in a constrained amount of time and are reconfigurable.
• Maximized security: Machines may be given risky tasks by the production line that pose a significant risk to the workers. Advanced security controls can also be put in place for components, machinery, people, and systems.
• Monitored control: The automated processes are controlled, monitored, and recorded to generate the big data that helps to identify patterns, improve operations, and implement changes to prevent future task errors.
The challenges faced in industrial automation sector
Despite the fact that industry 4.0 has primarily been adopted by large-scale businesses, there are still some challenges that the industrial automation sector must overcome. Some of these have been a hindrance to certain industries and are recurring in nature. The following challenges are seen in Industry 4.0:
a) Investment and infrastructure: Many industries have been operating for over 50 years. Changing the current technology and incorporating the new technology can be challenging at times and can involve huge costs if the necessary infrastructure is required and deciding which technology solution will turn out to be the most profitable.
b) Strategic planning: Before installing new technology in an existing setup, extensive strategic planning is required. A transition is required in terms of machinery and the change of mindset and automation process. Intelligent, detailed analysis is necessary to welcome automation in any running business.
c) Human factor: One of the main goals of automation was to reduce the risks associated with human intervention. Intelligent automatic inventions are no longer just tools but have become a workforce in itself. As a result, small, medium, and large businesses must train their employees on a regular basis and assist them in developing the necessary digital skills to keep up with changing industry trends.
The future prospects for industrial automation
Manufacturing has advanced to the point where businesses can only become more productive and efficient through innovation and technological enhancements to compete globally.
The IoT, interconnected machines, and smart factories are the main concepts of Industry 4.0. Manufacturers can leverage a wide range of features thanks to the interconnection of machinery, sensors, and control systems via intelligent networks. These include quick new product development, real-time production and supply chain network optimization, highly adaptable manufacturing, robust product and mass customization, self-optimization, self-configuration, and self-diagnosis.
Currently, the idea of industrial automation is based on having a single, centrally located “brain” that gathers data from manufacturing assets to aid in production decisions. However, decentralized intelligence is used in smart manufacturing, where every smart asset in the factory has access to all of their own data and is powered by enough processing to maximize their own productivity and efficiency.
Automation is expected to grow exponentially on a global scale in the coming years. At the same time, India is embracing Industry 4.0 at a reasonable pace and has seen exceptional growth as a result of recent automation advances. Industry 5.0 is a more recent trend that emphasizes immediate customer service, personalization, and the integration of humans and cobots (collaborative robots). To be proactive in the new industrial automation model and embrace new technological advancements.