After having achieved strong growth in recent years, India’s machine tool industry is faced with multiple challenges posed by the COVID-19 pandemic which has had a negative impact on various sectors including automotive, one of the key contributors to the growth. Whereas, several other external and internal issues including changing market dynamics and technology advances are having a ripple effect on the machine tool industry, forcing manufacturers to adapt to the new environment.
Machine tool manufacturers acknowledge that the prolonged global pandemic has posed many challenges for the industry. “It has rendered massive effects leading to decline in demand in the machine tool market,” says Prashant Sardeshmukh, Managing Director, MMC Hardmetal India Pvt Ltd.
As the COVID-19 continues to spell an unpredictable future for industry, Bijal Patel, Senior Digital Machining Specialist at Sandvik Coromant, says resilience will be needed if manufacturers are to navigate an economically and socially viable path. “Manufacturers must adapt existing processes, and do so quickly and cost-effectively.”
The pandemic aside that has had cascading effects across the industries, the machine tool industry has been facing multiple disruptions due to changing market dynamics and technology.
Industry players say the automotive sector has been one of the key contributors to the growth of the machine tool industry. However, the global developments in respect of emission regulations and rising concerns of climate change and sustainability have propelled the alternative mobility concept, vis-à-vis electric vehicles. “Although this transition is a long-term process, it has started showing impact on the machine tool industry,” accepts Sardeshmukh .
He explains the internal combustion engine needs high precision in machining of metal parts and a large number of metal parts are used. Whereas the electric drive trains have fewer machined parts.
As a result of that the demand for machine tools in the automotive sector may decline. “Reduction in car parts will lead to less throughput time and manufacturing facilities. This could lead to market shrinkage for the automotive cutting tools and machine tools,” explains Sardeshmukh.
Having observed the transformation of the automotive industry from internal combustion engines to electric drive trains, traditional machine tool manufacturers realise that they need to adapt to the changing market needs and prepare for the future.
Therefore, leading manufacturers are keenly observing the ‘green’ momentum in the automotive industry in order to make themselves compatible for manufacturing conventional fuel-based cars and hybrid cars.
In fact, many see the electric vehicle market as an area of opportunity.
J Prabhakar, Head, Machining Solutions Group (WIDMA) at Kennametal India Limited says they are working closely with their customers so that they can anticipate their needs and innovate to help them be more productive, efficient, and competitive.
“As automotive manufacturers expand their offerings of hybrid and electric vehicles, we are well positioned to support their evolving needs in this area,” he says.
For instance, the company has recently introduced a standard Vertical BTA machine for machining a shock absorber component for an electric two-wheeler manufacturer in India. “We have also supplied machines to a customer who manufactures and exports components to a German electric two-wheeler maker,” reveals Prabhakar.
Despite all the technological disruptions that are impacting the machine tool industry, Sardeshmukh believes there is a window of opportunity too. “The likely negative impact due to 3D printing and additive manufacturing may be limited in the near future. The cutting tool manufacturers may get good opportunities in the development of prototypes.”
He points out that cutting tool manufacturers are offering customised solutions instead of offering standard products. With the growing use of new materials and difficult-to-cut materials, Sardeshmukh says the cutting tool manufacturers are finding new opportunities to introduce special tools.
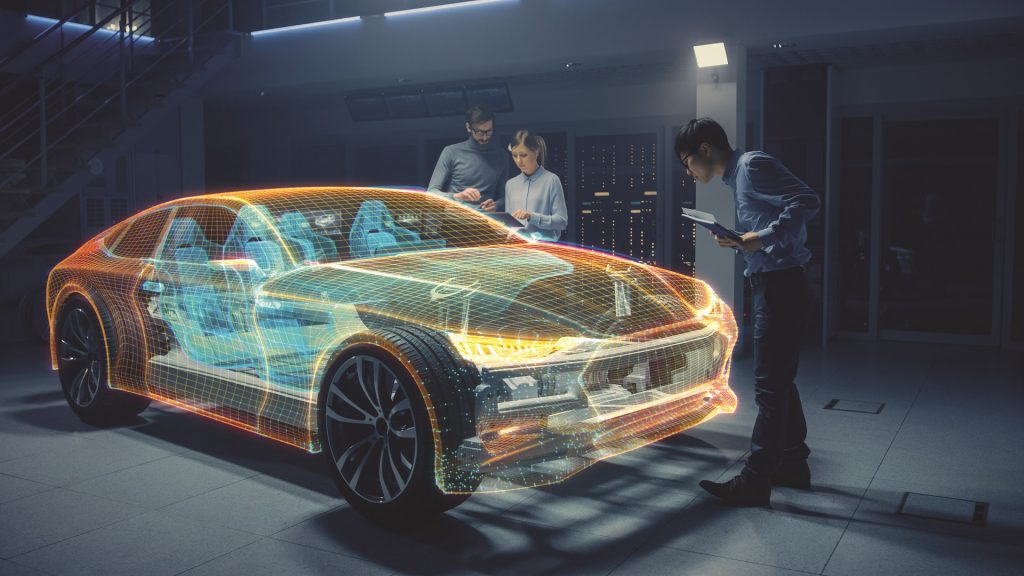
Top technology trends
Just like in other sectors, latest technological advancements are disrupting the machine tool industry, with the increasing integration of 3D printing technology with machine tools, technological advances in both hardware technology and software applications, and surge in automation.
This is forcing machine tool manufacturers to adapt to these trends with faster technology adoption.
Listing down some of these new trends, Sardeshmukh points out that technology in the offing is mainly about advancements in hardware and software. There will be more thrust on (i) inclusion of smart features and networks (ii) more automation and IoT-ready machines (iii) more use of artificial intelligence.
“The application of 3D printing in the machine tool industry is yet to be explored fully, but there are likely to be a lot of opportunities and challenges as well,” he says.
Currently, use of 3D printing technology in machine tools is limited to prototyping or for small series production. Many industries, particularly automotive, aerospace and defence go for 3D printing considering some advantages like lead time reduction, cost reduction and improvement in functionality. “Therefore, in the days to come these technologies will be adopted to optimum level in the machine tool industry, plastic and injection moulding,” says the MD of MMC Hardmetal India.
In fact, many machine tool manufacturers have begun to adopt integrated metal 3D printing technology into their CNC product mix.
As far as MMC Hardmetal India is concerned, Sardeshmukh says they are offering customised solutions instead of offering standard products. “In view of increasing use of new materials and difficult-to-cut materials, we are exploring new opportunities to introduce special tools,” he adds.
Industry players say the emerging technologies are mainly focused on making machines more productive, connected, and sustainable. “We are constantly enhancing our product capabilities to deliver solutions of the future,” says Prabhakar.
For instance, the company has introduced linear motors for axes movements in critical machining requirements to achieve best-in-class accuracy.
During the pandemic, its engineers leveraged virtual reality technology for equipment installations and commissioning when it was not possible to be onsite due to travel restrictions. “We continue to harness this capability for overseas installations as a way of working going forward,” he says.
Machine tool manufacturers are increasingly adopting IIoT in their machines for both historic and real time data monitoring to ensure optimum productivity and reliable performance through predictive maintenance to their customers.
Kennametal has recently integrated IIoT with its fixturing solutions that will help customers monitor and control critical parameters while the component is in the making, such as oil and coolant level and flow monitoring, air pressure monitoring, vibration detection on fixture body etc., to ensure desired output.
“We imbibe automation throughout the product manufacturing process, right from the design board, to commissioning and technologies such as remote diagnostics thereafter, enabling optimization of throughput and consistency,” says Prabhakar.
With relentless research and design innovations, the machine tool manufacturers are trying to deal with challenges posed by digitalisation and technological disruptions.
MMC Hardmetal MD says their efforts include extensive research for multitasking and additive manufacturing. “Besides, we strive for digital innovations, sensor integration, use of artificial intelligence (AI) and integration of modern simulation features to achieve high performance, productivity, precision and longevity of the product,” says Sardeshmukh.
With the growing discussions around smart manufacturing and Industry 4.0 which include use of advanced robotics, access to real-time data, IoT and so on, many machine tools manufacturers are dedicating their research and resources to bring in a lot of innovations in this direction.
Just a few years back, points out Sardeshmukh, CNC machines were seen only in the large scale industrial projects. “Today they are part of a small manufacturing setup as well. The CNC machines are increasingly becoming a part of smaller businesses and our households also.”
Leading solution providers such as Sandvik Coromant which offers CoroPlus® MachiningInsights says this platform is designed to give manufacturers greater visibility of CNC machine tools and machining processes, and to provide the tools needed to analyse, identify, and eliminate common sources of downtime and inefficiency. “Such a platform should prove useful as both Industry 4.0 and the Industrial Internet of Things (IIoT) accelerate the pace of change around machine connectivity,” says Patel of Sandvik Coromant.
Key drivers
With the activities in the automotive industry gradually returning to the pre-pandemic level alongside other sectors like aerospace and defence, electrical and electronics, medical devices, industrial machinery, and renewable energy are showing signs of positive growth, industry players expect the machine tool industry to perform in 2022 and beyond.
“I believe the machine tool industry will record robust growth and performance in the next few years. A survey indicates that the machine tools market in India can potentially grow to the extent of USD 1.9 billion during 2020-2024,” says Sardeshmukh.
The pandemic situation has caused a big setback to the machine tool industry because of prolonged lockdowns and frequent disruptions in labour availability. However, he says the manufacturing sector in India has gained a good momentum now. “The investors are preferring India over China and this will bring big opportunities to the machine tool industry.”
As far as key drivers are concerned, industry players anticipate that the fast-growing automotive industry, infrastructure sector, oil and gas, aerospace and railways will drive the growth for the industry.