Manufacturing is the bedrock of most major economies in the world. Over the decades, we have seen manufacturing companies trying to introduce changes in their processes – driven by the pursuit of productivity and cost competitiveness – faster, better and cheaper. As technology advances and more companies get access to it, companies’ ability to extract more out of their manufacturing capabilities will be tested.
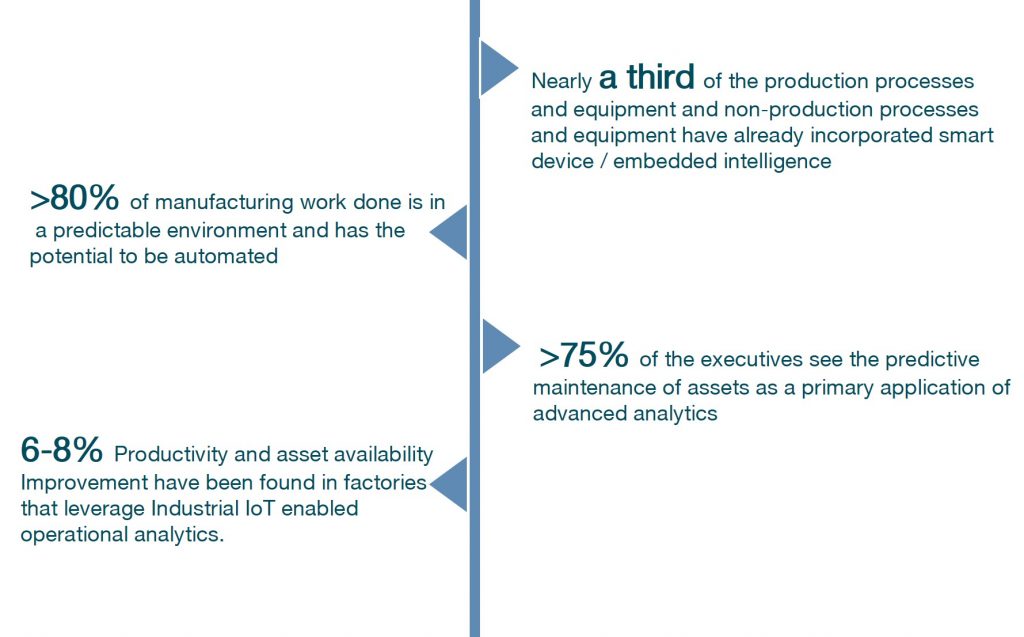
Smart and intelligent machines are slowly becoming a part of the world around us. Manufacturing organizations are looking for means to be more perceptive. Leveraging the technological advances of recent years, an enterprise that can sense the need of the market and consumers can “intuitively relate” to desired outcomes.
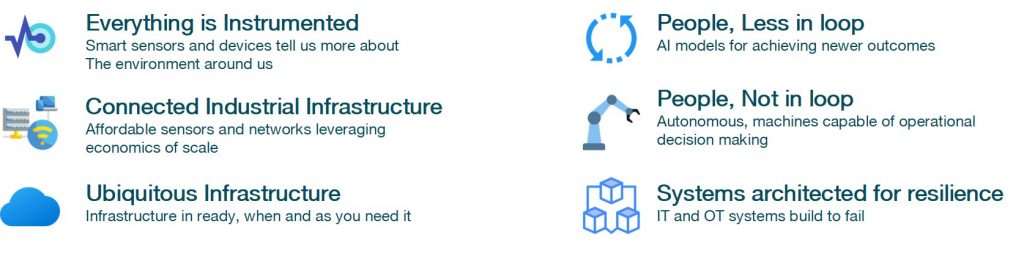
The dilemma that confronts most companies then is how they reconfigure their manufacturing processes and equipment as well as workflows to respond to any change with the least possible disruption and at speed. Of course, the future of manufacturing or ‘outcome-based manufacturing’ as we call it varies by industry – but if you look carefully, all of them have certain underlying fundamental themes. The key is to capture those common themes into a data product – a contextual unified data model. Thus, for any organization to get into modeling its manufacturing into a contextual unified data model, it must ask itself certain fundamental questions and have them answered.
De-centralized automation and intelligent / adaptive control
The first puzzle a manufacturing company must solve is ‘how could production lines be reconfigured to mix and match equipments in response to logistical issues or bottlenecks?’. For example: In a steel mill, say a company has six furnaces and three casters. Each caster has its own process capabilities. In the event of one of the casters breaking down, how could it leverage data and analytics to match the output of the steel melting furnaces to the other two casters so that customer delivery dates and requirements are least impacted.
Similarly, to ensure quicker and real-time decision-making, can data-analytics and simulation-based services enable a remote plant to take autonomous decisions while having negligible impact on the supply chain? A conscious and ‘hungry’ manufacturer would ask “could there be a way to predict a customer order and produce proactively without violating the inventory, cost, dispatch, or quality norms?”. This capacity to respond to unforeseen changes in customer demand and hence the production cycle will be extremely critical in the era of 10-minute deliveries.
Reimagined workforce (men and robots)
As automation gathers pace and urgency to respond to sudden changes becomes even more critical, companies will also need to reimagine the shopfloor that men and robots will share. The flow of materials will need to be optimized by continuously monitoring the material flow through the entire process cycle and deploying algorithms or similar tools. Information flow between man and machine, machine and machine and between man and man will need to be seamless.
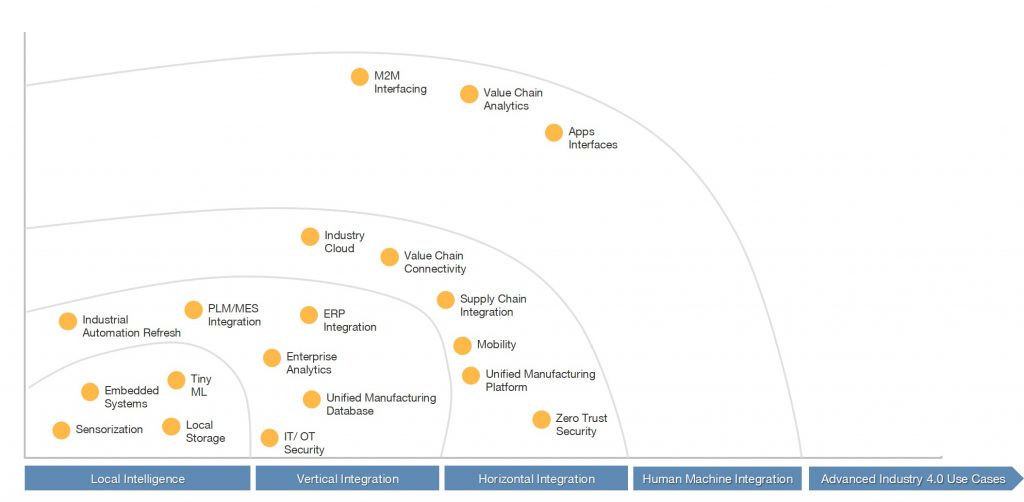
Agile Operations
Manufacturers are slowly getting into the age of mass customization or “batch size of one” in order to remain competitive and be able to uniquely fulfill the customers’ requirements. This is true for both B2C and B2B scenarios. Integrating emerging technologies like AR/VR, 3D printing and numerical simulations along with a closely linked value chain – all in a single unified data product – is fundamental to achieve “batch size of one” capabilities for the manufacturers. Cross pollinating traditional manufacturing methods with 3D printing holds the key and organizations must start preparing for this new manufacturing paradigm.
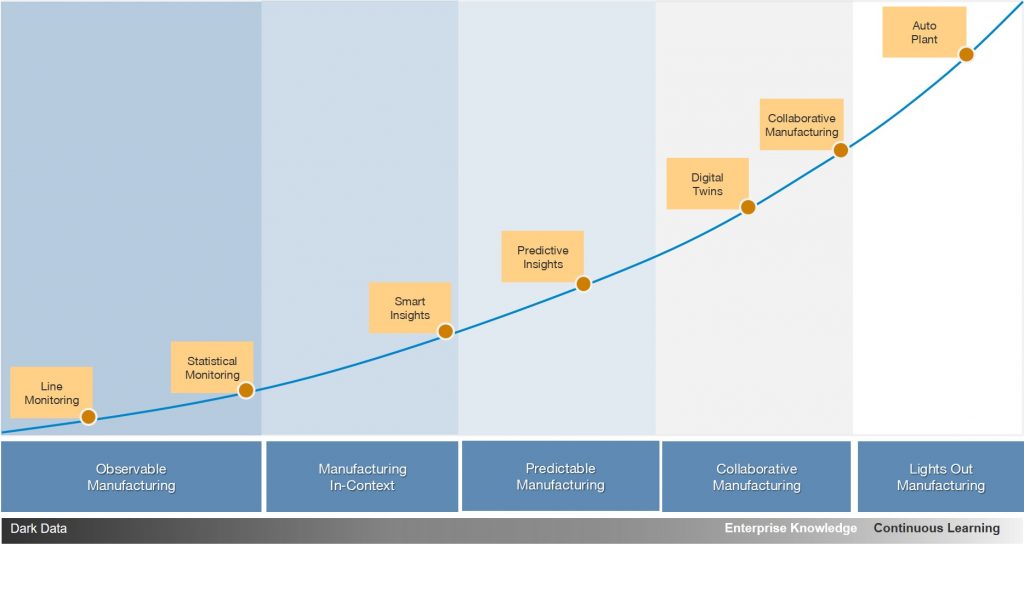
Operational analytics and process monitoring
In most cases, sharing of information between various actors involved in the production processes would be possible by combining the knowledge of customer requirements, previous production records and prescriptive data analytics. If downloaded on the machines, work instructions to operators could be passed on for further action.
Repair and maintenance of plants and machinery in any factory is a given. It can take a few days to a few weeks, depending on the kind and size of machinery and operations. In a situation where the cost of capital remains elevated and companies look to get more bang for their buck, idling the plant and machinery for long periods may not be feasible or at least desirable. Such a situation would warrant timely determination of the condition of assets that are in operation to predict when maintenance should be undertaken.
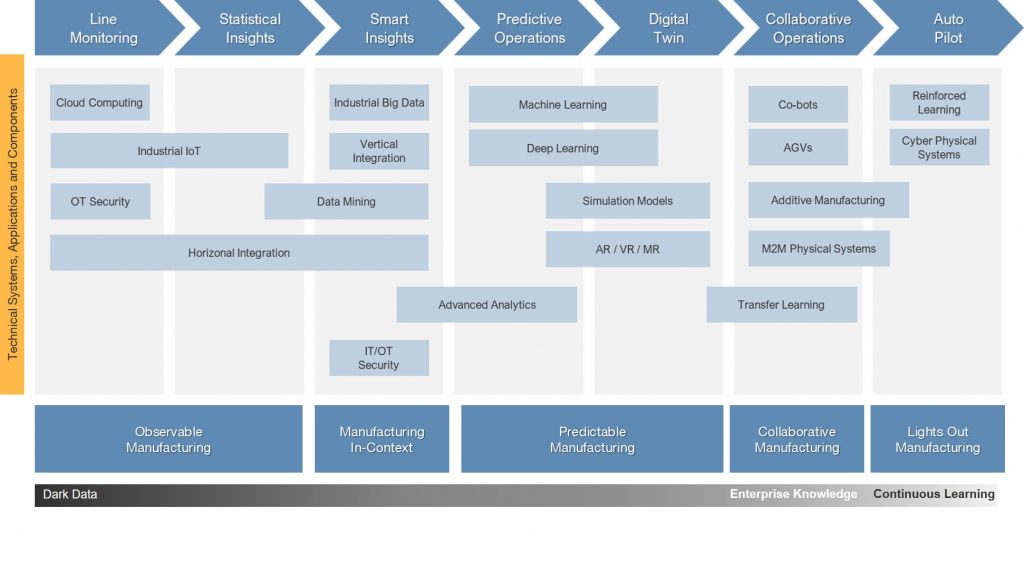
Everything mobile
A fast-developing issue that companies these days are addressing with respect to their manufacturing processes is ESG – how do they limit the damage to nature and society and make their processes In a social media-driven world where news travels fast and where consumer tastes and awareness are rapidly evolving, it is a matter that can’t be ignored. Capturing data related to the location of individuals and exposure to hazardous and lethal materials in a plant will be required. Mobile-based intelligent solutions will need to be implemented so that record keeping can happen as part of the process compliance without affecting the workers’ productivity.