In process engineering, the exact observance of pressures in vacuum-assisted processes is an important parameter for ensuring optimum efficiency and the best possible product quality. VACTEST vacuum measurement equipment from Busch is designed to combine the latest advances in vacuum measurement technology with exceptional manufacturing quality – providing an innovative and comprehensive portfolio of active vacuum gauges and controllers. This makes it possible to match the right measurement technology to each and every process.
Robust construction, reliability and measurement accuracy are key features of these devices, making them the ideal choice to monitor and control your vacuum process, whether it is in industry or research. These state-of-the-art technologies allow a wide measurement range from 1600 to 5 · 10-10 millibar covering all vacuum levels with accuracy. All sensors comply with international standards and regulations such as CE and RoHS.
A number of different sensor technologies in the VACTEST series cover the entire range between rough vacuum and ultra-high vacuum. They can basically be divided into two main categories: direct and indirect pressure measurement. The direct measurement principle is independent of the process gas and is based on the pressure that the molecule flow exerts on a membrane. This method is mainly used for rough and medium vacuum processes. At a higher vacuum level, indirect measurement principles are used, based on special properties of the process gas, such as thermal conductivity or ionization probability. Unlike the direct measurement method, these principles depend on the type of process gas. For this reason, a specific correction factor must be applied for each process gas – except for air and nitrogen.
A number of factors must be taken into account when selecting the correct sensor. In addition to the process and ambient conditions, the pressure range, required accuracy and gas composition play a key role in achieving optimum measurement results. With three product lines available, Busch VACTEST meets the accuracy, measurement range and functional requirements of every vacuum system or process.
VACTEST digital transmitters are high-end gauges coming with a full range of options as standard. Their intelligent micro-controller architecture allows optimum sensor control, as well as many setting options, making them the ideal solution for a variety of applications. VACTEST digital transmitters are based on Pirani sensor technology or on combinations of Pirani / cold cathode or Pirani / hot cathode technologies.
VACTEST analog transmitters feature a compact, rugged and functional design. Thanks to their excellent measurement accuracy and stability, these transmitters are ideal for centralized monitoring and control systems.
VACTEST mobile gauges are the perfect hand-held solution for quality assurance with vacuum processes and maintenance. These battery-operated gauges offer various functions, such as a USB interface for data export and display, as well as a data logger. They can even be used under a vacuum. For example, these gauges can be sealed in vacuum packaging to measure the pressure within the packaging.
VACTEST active sensor controllers, which are compact control units designed for the simultaneous operation of several vacuum gauges, round off the product series. Used either as a table-top device or rack-mounted, they allow intuitive menu navigation and ensure full control of each transmitter. Parameters, such as gas type correction factor, pressure units, setpoints and other beneficial functions are easily adjustable.
In addition to the measuring devices, the VACTEST Viewer is also available. It is a free Bluetooth monitoring application for mobile devices with an Android operating system. It can be used to display the pressure values of up to 16 connected sensors. The tool was designed for Bluetooth data exchange between software and sensors and is ideally suited for maintenance and calibration purposes. Visual and sound alarms can be preset for maximum and minimum pressure values.
Monitoring and control of vacuum processes made easy
SHARE
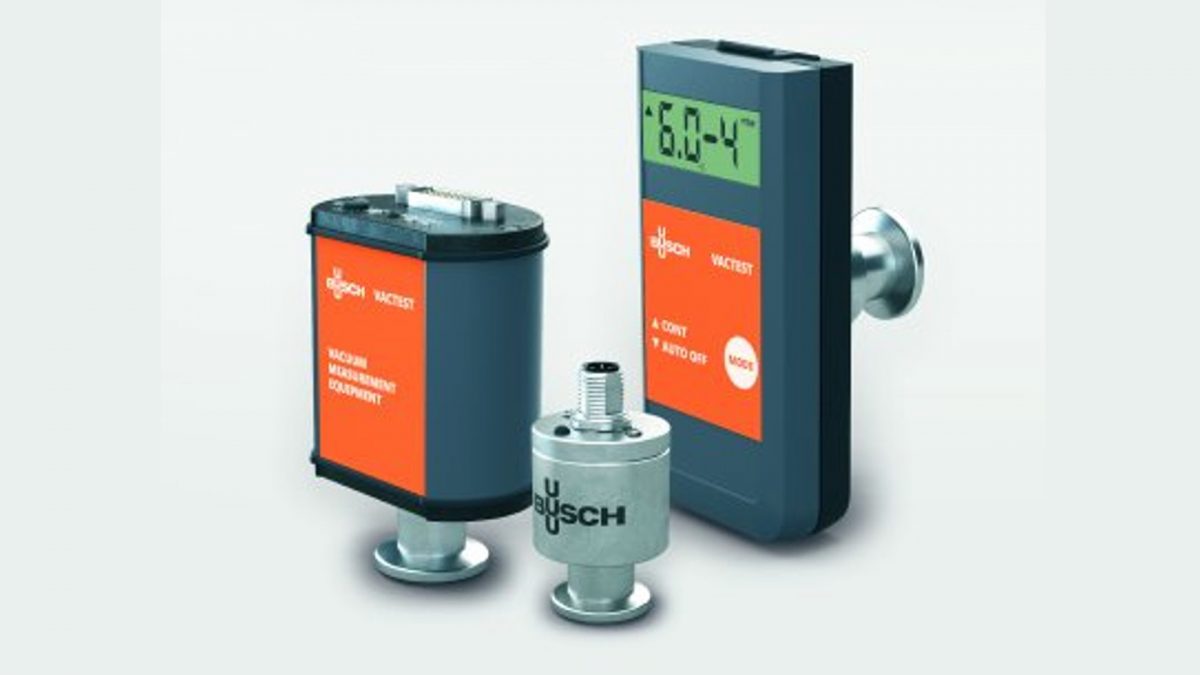