Mercedes-Benz will build ultra-high-performance axial-flux electric motors at its Berlin site as the luxury car brand prepares to go all electric by 2030, where market conditions allow. With the transformation of the Berlin site, Mercedes-Benz will reach new digitalisation and electrification milestones on the way towards a sustainable and emissions-free future.
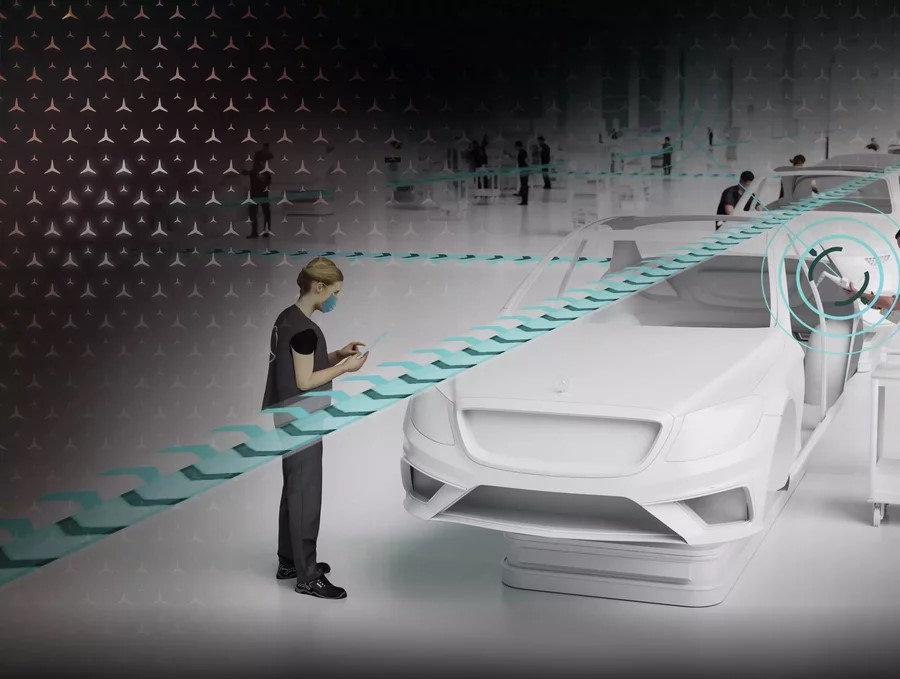
By insourcing further electric drive components, the Berlin plant is charting a new course for its future and expanding its portfolio of products. Mercedes-Benz announced the acquisition of YASA, UK-based manufacturer of ultra-high-performance electric motors in the summer of this year, securing access to unique axial-flux technology, deepening its vertical integration and value creation in development and production. The portfolio of the Berlin plant already includes assembly volumes of electric drive units and the so-called EE Compartment.
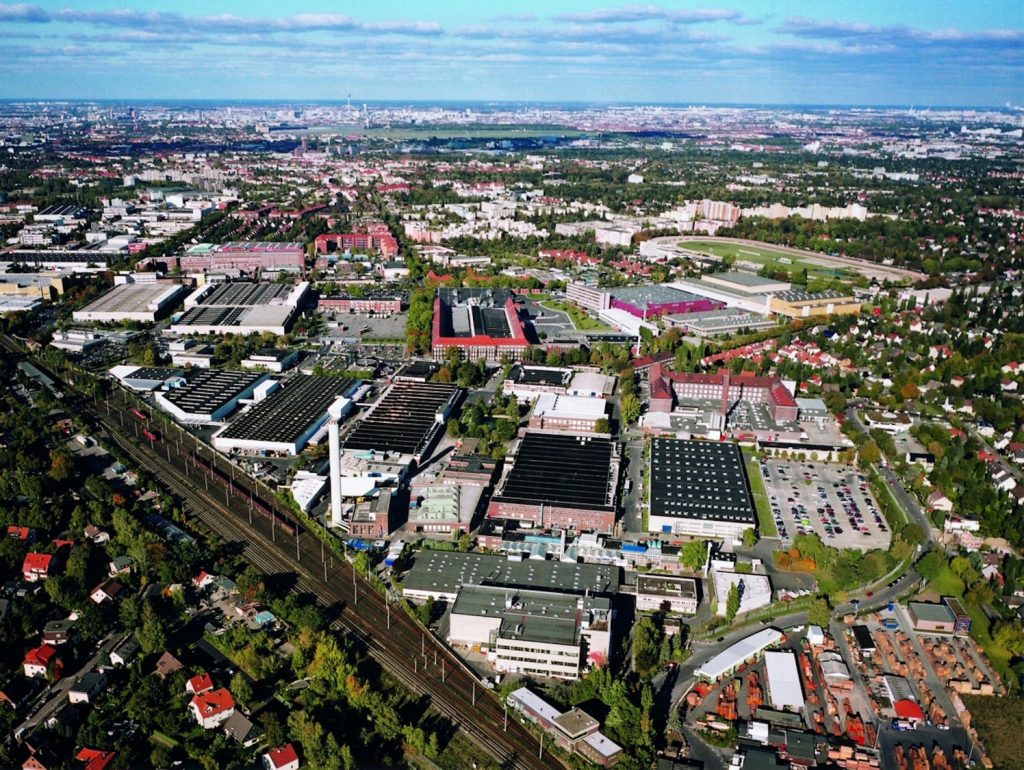
In addition, the build-up of the Mercedes-Benz Digital Factory Campus – a campus for developing, testing and implementing pioneering MO360 software applications – has reached an advanced stage. A series of state-of-the-art pilot lines will go into operation next year. Berlin will become the competence centre for digitalisation in the global Mercedes-Benz production network and support the worldwide rollout for new releases and apps in the MO360 ecosystem. At the same time, the campus will become a MO360 training and qualification centre with innovative approaches in the area of digital implementation. Mercedes-Benz is investing a low triple-digit million euros amount in the transformation of its Berlin plant within the next six years.
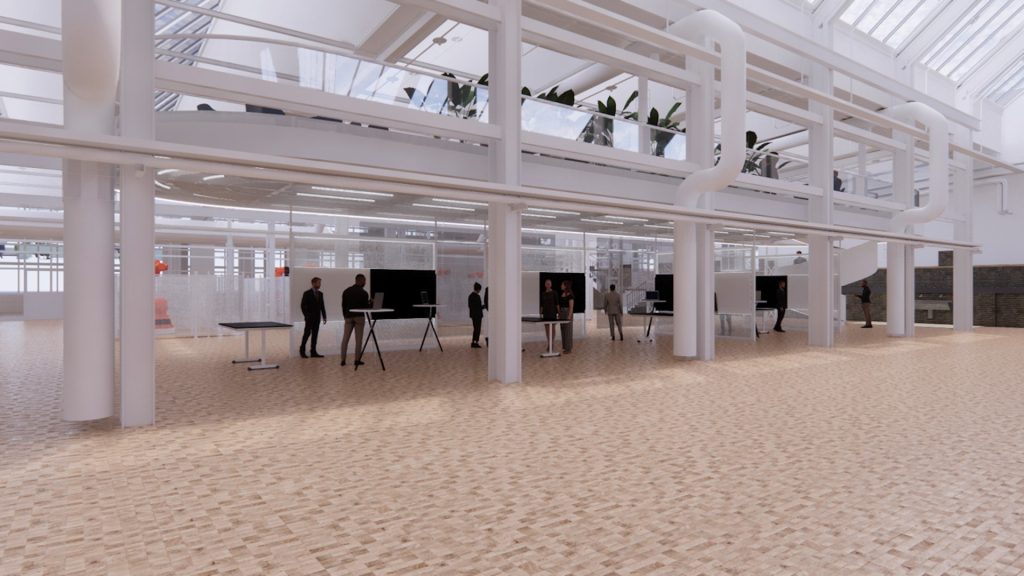
“The transformation of the automotive industry is more evident at our Berlin site than at any other Mercedes-Benz plant. The transformation from a production site for purely conventional drive components to a competence centre for digitalisation and production in the field of e-mobility is a significant step for us and our employees. We are offering groundbreaking new opportunities for this traditional location and underlining its role in our global production network – not least as a decisive driver of our digitalisation offensive. With the production of high-performance electric motors, the Berlin plant will become a key pillar of the sustainable Mercedes-Benz electrification strategy,” said Jörg Burzer, Member of the Board of Management of Mercedes-Benz AG, Production and Supply Chain.
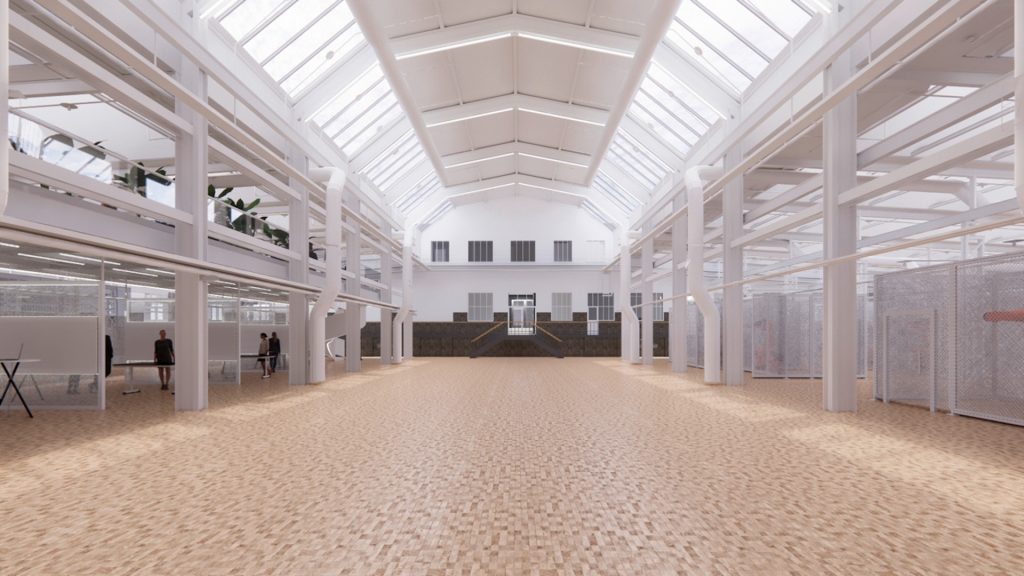
Berlin will become the hub for global Mercedes-Benz training and qualification activities. Future training programmes for the entire production network will be developed and implemented in Berlin using an innovative and flexible digital learning platform. Furthermore, the portfolio of qualification activities has been redefined. Going forward, the qualifications will include, for example, an IT specialist for digital networking and IT specialist for data and process analysis.
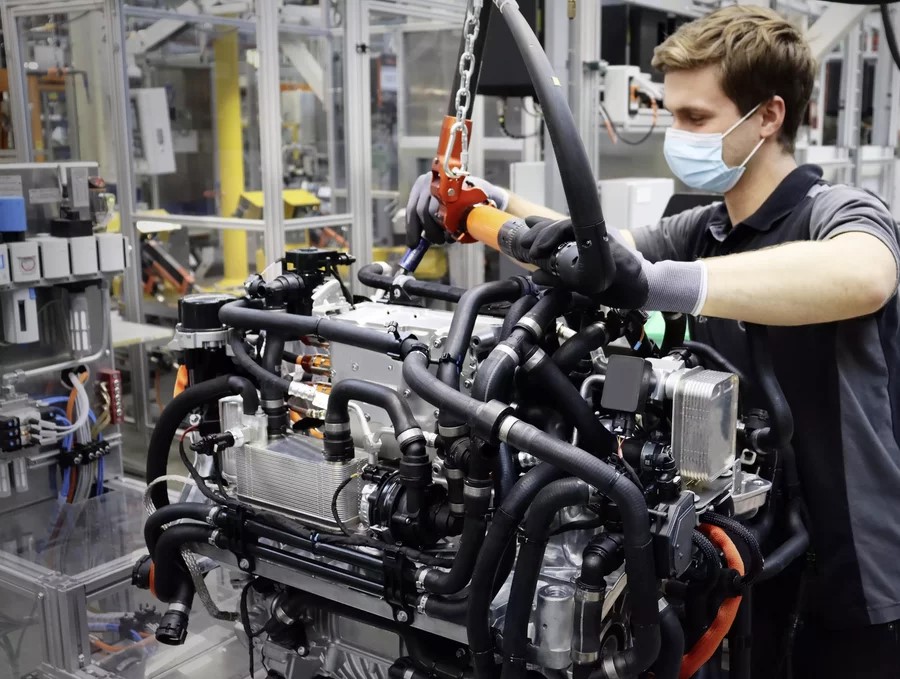
A new qualification programme, designed to give production staff new opportunities, was tailored to create new digital employment profiles for Berlin. As part of a pilot project, production staff are being trained up for new digital jobs, allowing them to play an active part in shaping the transformation. A particularly good example of this is the new profile of Junior Software Developer for the Mercedes-Benz Digital Factory Campus.
The transformation of the Mercedes-Benz plant will advance through a process of mutual cooperation between employee representation and management. The mutual agreement struck between the works council and management includes both structural and personnel measures. The focus will be on retraining and requalification measures for employees at the site, while at the same time taking advantage of natural staff turnover including retirement and buyouts. The main priority is to implement these structural and personnel measures, which impact employment profiles, in a socially acceptable manner.
MO360 – The digital ecosystem
The digitalisation of production is an important success factor for Mercedes-Benz. The digital MO360 ecosystem was launched last year. Large parts of the modular and expandable system are already in use at around 30 Mercedes-Benz plants worldwide. As a competence centre for digitalisation, the Mercedes-Benz Digital Factory Campus will drive the development, testing and validation of future software applications and concepts for MO360 from next year onwards – in a real production environment. The aim is take the new developments tested in Berlin and to roll them out worldwide and to qualify the users in the plants.
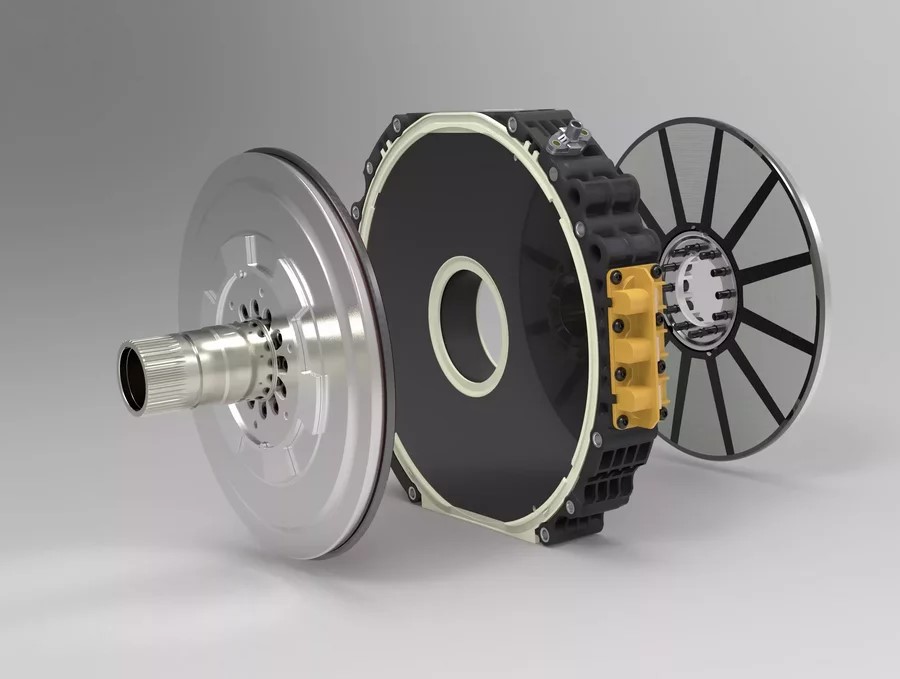
The highlights of MO360 include:
- Increase in production efficiency through the use of MO360
- Different tools combined into one tool family with a unified user interface
- Digital Shopfloor Management to help organise production
- Digital Worker Assistance to support assembly activities
- Quality Live is all about product quality
- The MO360 Data Platform provides the fundamental basis for workers to access and analyse all data in their field of responsibility, regardless of their IT skills. The MO360 Data Platform is the “digital twin of production”. It makes a decisive contribution to the democratisation of data and, with the help of artificial intelligence and predictive tools, supports the qualification of employees in the context of the transformation.