Manufacturing 4.0 is the dawn of machines that can think, learn and make decisions on their own. The idea isn’t strange to us because we’ve seen similar machines in movies. We have seen the T-800 in Terminator 2 and the NARS and CASE machines in Interstellar. These machines reflected human emotions, including the need for authority and even humour. These machines filled us with a mix of delight, thrill and curiosity. What new could be possible with this generation of machines?
Fast forward to 2023 and the real world. The machines of the future are here! Manufacturing 4.0, also known as Industry 4.0, refers to the fourth industrial revolution. The term emphasises the integration of advanced technologies such as artificial intelligence, the Internet of Things (IoT), and robotics into manufacturing.
Traditional manufacturing is grappling with challenges to cater to the ever-changing demands of a rapidly evolving industry. One of the biggest issues manufacturing companies often face is a shortage of skilled labour, as most manufacturing processes in India are traditional and labour-intensive. On top of that, customer demands are also rapidly changing, often leaving manufacturing companies struggling to keep up with the pace. Supply chains, too, lack efficiency. Lack of transparency is another issue manufacturing businesses have to tackle.
The only way forward for manufacturing companies is to embrace new technologies and adopt modern practices to increase efficiency and productivity. The innovations have brought to life Manufacturing 4.0 – powered by Artificial Intelligence and Machine Learning technologies.
Key pillars of Manufacturing 4.0
Manufacturing 4.0 comprises four key pillars:
- Interconnectivity: the integration of physical and digital systems. In the Industrial Internet of Things (IIoT), sensors are attached to physical objects. Those sensors collect real-time data from physical equipment, machines, and devices and transmit it to digital systems for analysis and decision-making.
- Automation: using advanced technologies such as robotics and IoT devices to automate tasks and processes. Automation is expected to increase productivity by up to 40% by 2035. Intelligent robotics is used by businesses to automate manual tasks. A European vehicle factory, for example, linked robots to efficiently manage process flow and collect the data required to monitor the process, improve production flow, and decrease losses.
- Machine Learning: Let’s understand the role of ML with an example of how machine learning impacts Manufacturing 4.0 through quality control. Machine learning algorithms can analyze sensors’ images and data to identify product defects as they move along the production line. This allows for real-time adjustments to be made to the production process, reducing waste and improving the overall quality of the final product.
- Real-time data: the data generated by sensors and other sources is collected and processed in real-time to provide actionable insights to optimize the manufacturing process. For example, in the energy industry, sensor data can monitor the health of wind turbines, solar panels, and other equipment. These can be analyzed to predict when equipment is likely to fail, allowing maintenance to be scheduled before it becomes critical.
How can Manufacturing 4.0 be a game changer?
By now, you might be curious about how AI/ML can be used to ramp up efficiency, cut costs and transform the industry. Here are some ways manufacturing 4.0 can turn the tables and shake things up.
Digital Twin: AI and digital technology are making forays in manufacturing by creating digital replicas of assets and processes known as Digital Twins. With digital twin powered by Artificial Intelligence, you can create digital models of your industrial assets. Through these models, you see complex manufacturing processes from start to finish, helping you spot where problems might arise before they happen in real life.
The Digital Twin technology can generate predictions to identify suspected issues and provide recommendations on solving them while factoring in efficiency and maintainability. By better planning out maintenance tasks and further leveraging automation with digital twins, companies can reduce the costs associated with downtime and maintain higher margins and overall equipment effectiveness (OEE).
Bosch IoT Things, a cloud service, provides a digital twin/management shell for physical assets. The company offers a range of IoT solutions and services that support the creation and management of digital twins, including the Bosch IoT Things platform and the Bosch IoT Hub device connectivity layer.
Smart Factories: Fitted with an interconnected network of machines, communication mechanisms and computing power, smart factories leverage the powerful combination of these tools to achieve optimal operational efficiency. This system also utilizes cutting-edge technologies, including artificial intelligence (AI) and machine learning, enabling it to analyze data and drive automated processes while adapting and learning.
One example that particularly pops up in mind is that of the BMW plant located in Regensburg, Germany. The factory utilized various cutting-edge technologies, including robotics, 3D printing, and smart data analytics. The automobile giant significantly streamlined its production processes and improved quality. Specifically, the company reported that the deployment time for new applications was reduced by 80%, and the number of quality issues decreased by 5%. The World Economic Forum dubbed the Regensburg plant a “factory of the future”.
Supply Chain Optimization: There are various applications of AI and ML, and different ways they can be operationalized throughout the supply chain. A lot of information in the supply chain is transacted through documents such as BOL, POD, contracts etc, AI can easily digitize them. Thus, reducing human error and enhancing the customer experience. COVID-19 showed us how important it is to have visibility and connectivity across each node in the supply chain, to manage uncertainty and unpredictability. While one of the most important steps to connectivity is supply chain digitalization, AI, combined with blockchain technology, can strengthen end-to-end integrations and connect key activities in the supply chain.
Enhanced productivity: Implementing Industry 4.0 solutions can substantially improve and benefit both the manufacturer and its customers. These solutions can lead to reductions in machine downtime (30-50%), increases in throughput (10-30%), improvements in labour productivity (15-30%), and more accurate forecasting (85% more accurate).
As technology progresses, digital transformation offers an unprecedented opportunity for manufacturers to innovate how they work – affecting people, processes and productivity.
Final thoughts
Manufacturing 4.0 is the future, and it’s clear that, more than ever, stakeholders must work together to transition as quickly and effectively as possible. The immense benefits of embracing these innovative technologies are far too great to ignore, with improved efficiency, customer experience, decision-making, and a safer and better empowering work environment for employees all on the list.
To make this happen, manufacturers, technology providers, government agencies and academic institutions must unite forces. Likewise, players in the private sector must invest in research and development to drive innovation, while governmental support is critical. So the time to act is NOW. Let’s join hands and lead the way towards a future where industry and innovation seamlessly merge, creating a new era of manufacturing that will elevate us all.
Author:
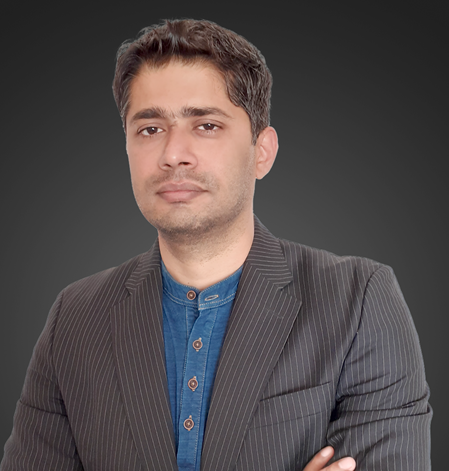
Puneet Vinod Kumar, Vice-President-Tech, Moglix