Sanat Vajpai, India Business Manager – Intelligent Devices at Rockwell Automation, says productivity optimisation, downtime minimisation and energy efficiency remain major trends fuelling the growth of drives and encoders. “This is due to the sustainability push by the India government and corporate businesses.”
He explains the mega trend of digital transformation needs data at its core, and this requires intelligent and connected devices on the field like variable frequency drives (VFDs) and encoders along with sensors.
Modern intelligent drives are a key technology for the fourth industrial revolution, because they enable the coordinated operation of networked, decentralised, and autonomous production processes, agrees Amit Deokule, Sr. GM- Sales & Marketing, NORD Drivesystems Pvt. Ltd.
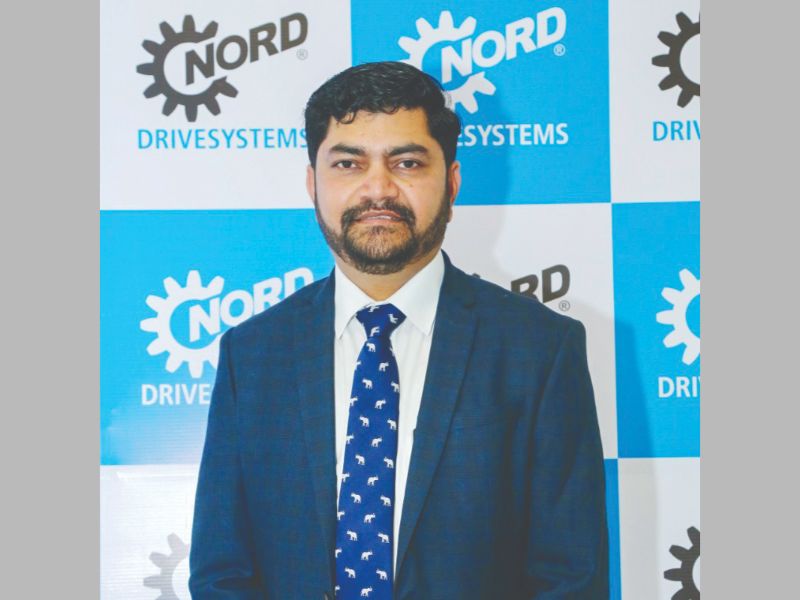
With the PLC which is integrated into the NORD frequency inverter, he says application-specific functions close to the drive unit can be efficiently programmed and parameterised in the same way as other frequency inverter functions.
Even though this industrial development is still in its infancy, Deokule explains that the development perspective is toward cyber-physical systems, which operate decentrally, independent of their particular manufacturers and across various locations.
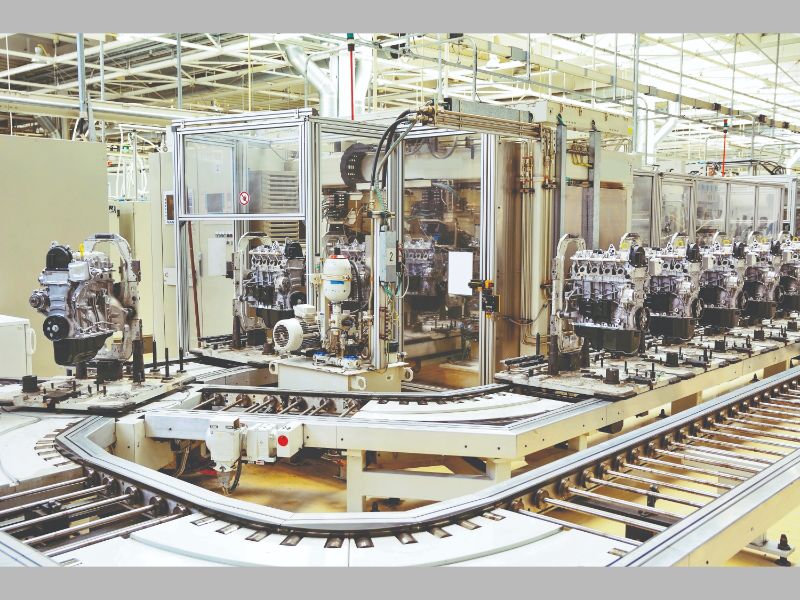
“Encoders play an integral role in almost every mechanical system that involves motion monitoring or control. The frequency inverters ‘speed control is extremely precise thanks to sophisticated and fast measuring methods and calculation algorithms in combination with integrated high-precision current vector control,” he adds.
To address the demanding drive applications, points out Sameer Gandhi, MD of OMRON Automation India, there is more inclination towards coordinated common DC bus solutions against traditional standalone drive solutions.
Besides increase in productivity, he says it gives valuable advantages of energy conservation, simplified wiring and panel design.
Also, Gandhi explains there is an increasing trend to offer integrated safety functions within the drives which gives advantages such as fewer control components than typically required for traditional safety circuits, reduced engineering time to develop those circuits, less cabinet space for housing components, and shorter assembly wiring time.
“There is an inclination towards connecting drives to the plant network intelligently so as to get benefits of the Industrial Internet of Things (IIoT),” he says, adding that using the IIoT, drives’ data can be collected and analyzed to help the business optimize processes, manage energy consumption, and minimize costly asset downtime.
For encoders, Gandhi says, the industry is moving towards more reliable and accurate solutions and also considering adopting IO-Link enabled solutions which are an integral part for realizing Industry 4.0 based transformation.
IO-Link is a low-cost, easy-to-implement communications system designed to simplify connections between large-scale fieldbus or industrial ethernet networks and sensor or actuator devices located on the factory floor.
As technology evolves, with incorporation of the latest trends and advancements, industry players say drives and encoders can now accurately provide feedback for position, speed, and direction. This increases the accuracy and reliability of manufacturing processes.
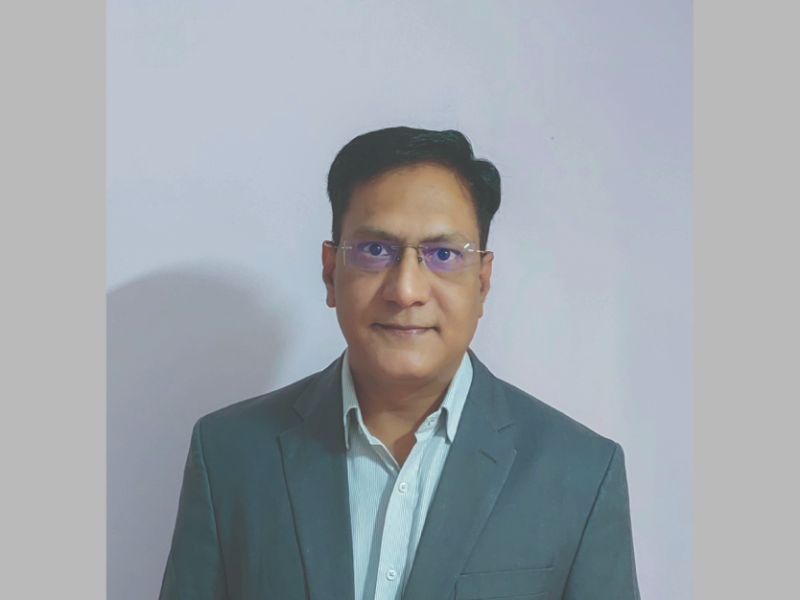
“The drive technology requires compactness, harmonic and regenerative solutions as part of energy optimization, transformation from general purpose motor control to advanced vector controls, advanced built-in compatibility of high-speed networks, AI (Artificial Intelligence), lifecycle diagnosis, safety features and maintainability,” says Ravikiran Talwekar, Inverter Marketing Head- Factory Automation & Industrial Division at Mitsubishi Electric India Pvt. Ltd.
With the innovative designs, the drives and encoder systems help accomplish features like modularity, interoperability, and significant space savings, says Himanshu Sharma, Manager – Marketing & Communications at B&R Industrial Automation.
He says the most advanced drives and encoder systems also incorporate integrated safety technology, enabling intelligent responses to potentially hazardous situations. “Manufacturers can undoubtedly increase their production efficiency, save energy, and reduce downtime and operational costs by implementing cutting-edge drives and encoder system technologies.”
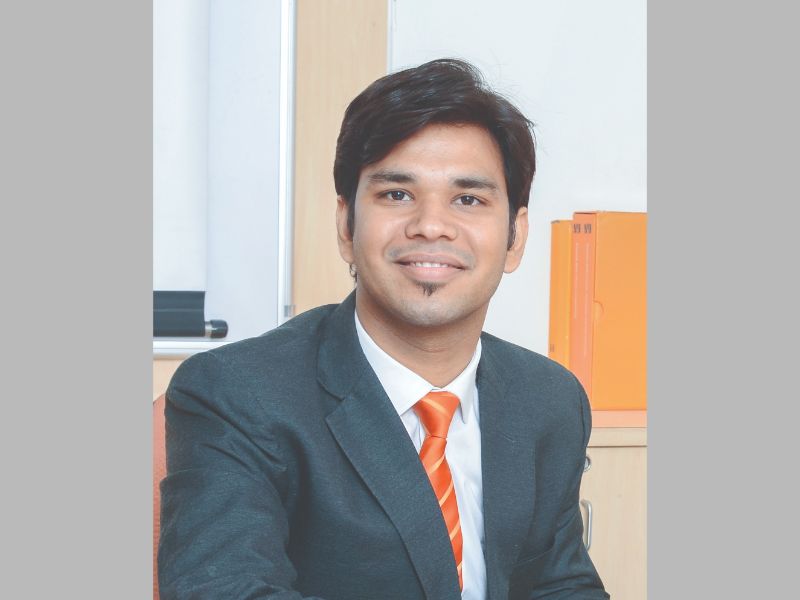
For Vajpai of Rockwell Automation, a well-connected drive provides a wealth of data and information about the process and machines. “Flexible manufacturing requires fast and automated motion control, leading to the need for more applications and machines to drives and encoders,” he says, adding that the growth can also be attributed to the emerging need for accuracy, precision, and control in the industrial sector.
Types of drives & encoders
There are several different sensing technologies that may be used within an encoder to detect the motion or position.
Talwekar of Mitsubishi Electric says rotary encoders are incredibly diverse and are used across many different industries in various applications. The common sensing technologies used in encoder include: “Optical” -most accurate to the sensing, “Magnetic” Hall sensors – effective sensing through changing magnetic field, “Capacitive” — a relatively new sensing technology, the change in capacitance using a high frequency reference signal.
“Whether incremental or absolute, encoders track motor shaft rotation to generate digital position and motion information. The type of encoder for industrial automation processes depends on the requirements for monitoring the movement and position of an object in various environmental conditions (hazardous and non-hazardous),” he explains.
Mitsubishi Electric says its drives are strongly capable of the automation process to enhance the highest efficiency and productivity of manufacturing units. Its dedicated drives for respective applications support quick installation and seamless operations of the process.
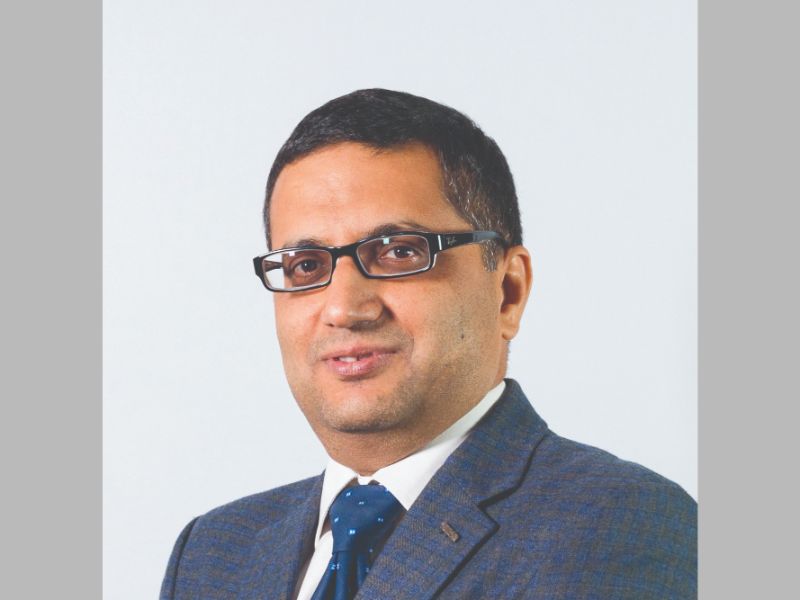
OMRON’s Motion & Drives portfolio primarily consists of Servo Systems, Motion Controllers and Frequency Inverters — all of which Gandhi says bring in value to the shop floors in the form of speed, accuracy, space saving, and flexibility while meeting specific load conditions with reliable and customized technology.
“All the solutions are customizable. Our encoders mainly consist of Rotary Encoders. They play an important role in measuring the number of rotations, the rotational angle, and the rotational position,” he adds.
Rockwell Automation has PowerFlex AC drives in both low and medium voltage power ratings. “We also have Kinetix servo drives for motion control applications in single axis or multi axes. Both AC and servo drives provide flexibility, productivity, and ease of use,” says Vajpai.
B&R says it offers a comprehensive portfolio of innovative motion control products comprising servo drives, stepper drives, variable frequency drives, servo motors, stepper motors, and integrated digital multi encoder interface cards. “We are helping Indian manufactures and our partners by incorporating our drives and encoders system, so that they can meet growing demands of increased productivity and availability while achieving perfection,” says Sharma.
Adoption rate
High-end automation with technological advancements, Industry 4.0 and IoT are penetrating the market to enable various industrial processes to adopt automation, says Talwekar of Mitsubishi Electric.
It is estimated that by 2025, 80-85% of manufacturing units in India will get automated. Using Mitsubishi Electric FR-Series Drives with advanced technology, he says manufacturers can have many advantages to achieve a seamless automation process:
The adoption rate of new technologies like advanced corrosion resistance, predictive analytics on-board drive, remote operation of drives, are still low in India as compared to other markets in regions like Europe, the Middle East, Africa, North America, and some Asia Pacific countries as well, says Vajpai.
On the other hand, he adds the adoption of drives at large for energy efficiency or high-performance motor control is good and growing due to operational needs and the national environmental, social, and governance (ESG) push.
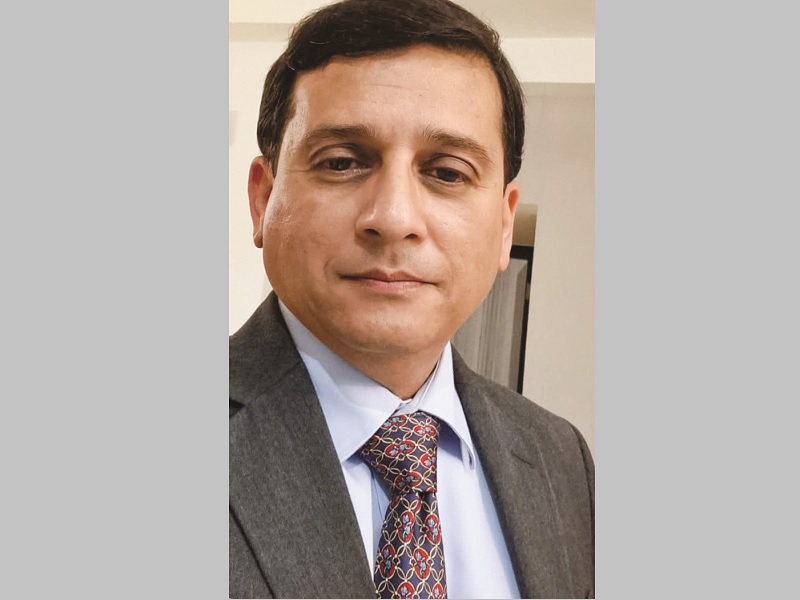
“These new technologies will help to increase product lifetime, reduce mean time to repair and unplanned downtime, and provide fast and reliable data from drives in a cyber secure manner, improving profitability and competitiveness of Indian manufacturing in global markets,” adds Vajpai.
Post pandemic, there has been a V-shaped recovery, points of Gandhi of OMRON. “It’s building up gradually and the sentiment has been quite positive. The manufacturers are realizing the utility of technologies to turn their factories smarter and connected and capable of handling their biggest challenges like reducing downtime, decreasing frequency of sudden failures, improving changeover efficiency and real-time data based predictive maintenance.”
He says this applies for encoders and drives too since they play an important role in automating and delivering precise speed and direction to ensure that motors run safely and smoothly. With mid-sized and large manufacturing plants enhancing their investment in automation solutions, Gandhi explains encoders & drives business is seeing a rise for better utilization of assets, controlling the quality of end products, and minimization of errors.
Demand drivers
The increasing demand for advanced industrial automation in various industries like automotive, electronics, pharmaceutical, F&B, packaging, and aerospace is driving the demand for controllers, drives and encoders, say industry players.
Sharma of B&R Industrial Automation explains these industries are required to measure the speed, torque, and position of parts in a wide range of applications.”
Rockwell Automation points out that automakers in recent years have automated their plants to reduce the number of issues on the factory floor, improve efficiency, and reduce operational costs. With electric vehicles becoming a key growth contributor to the automotive sector, Vajpai says it is one of the major sectors that will drive the demand for automation, drives and encoders.
Mitsubishi Electric says manufacturers are expecting to implement advanced drives compatible with AI technology solutions and rotary encoders for efficient and productive manufacturing processes. Talwekar says many key industry sectors are demanding such high-end automations. “Automobile, Warehouse, Electronic, Converting, Elevator, Steel / Metal, Textile, Material Handling, Construction, Cement, Pharmaceuticals, F&B, Water transportation, Port, Mining, Aerospace and other prominent industries are demanding high-end automation to encourage efficient, safe and productive operations.”
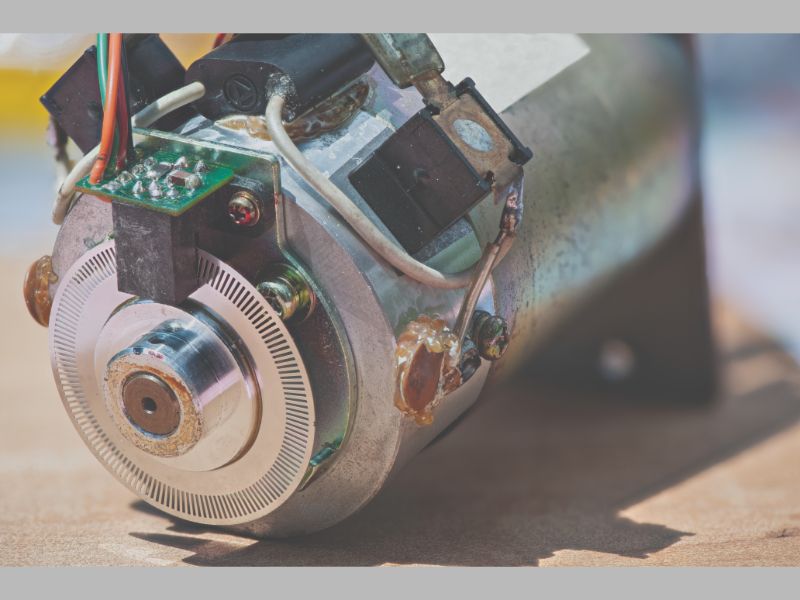
Owing to their need for 24/7 connectivity to production lines, Gandhi outlines that the focus industries for encoders and drives are food & beverage, pharmaceutical, automotive, and machine tool industries. For dives specifically, he adds the application-based segments like packaging, material handling, inspection along with robotics in the automotive and food & beverage manufacturing sector are the key growth drivers while for encoders, machine tools, packaging, textile segments play an important role.