The cold forming industry in India has been growing significantly over the years, mainly due to the demand from the automotive sector. With India’s auto components industry expected to reach USD 200 billion by FY26, contributing to 7% of the total GDP, this industry continues to demonstrate a promising outlook.
Cold forming is a manufacturing process that plastically deforms metal using dies. It allows for high-speed production, generates little to no waste of material compared to conventional machining for the same geometry, and creates a stronger end product due to the work hardening of the material. The major advantages of cold forging are improved mechanical strength, close dimensional tolerances, good surface finish quality, efficient raw material use, high production rate and low overall cost. The cold forming process, which allows the conversion of raw material into any desired shape at ambient temperature, is used in many sectors, such as infrastructure, defense, healthcare, and railways, which are currently witnessing significant investments in India.
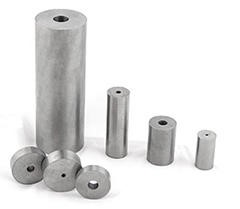
Cemented carbide application in cold forming
The forging industry is increasingly adopting cold forming to manufacture components with a high degree of dimensional and structural precision that undergo high mechanical stresses to achieve “net shape” or “near net shape” and better surface quality.
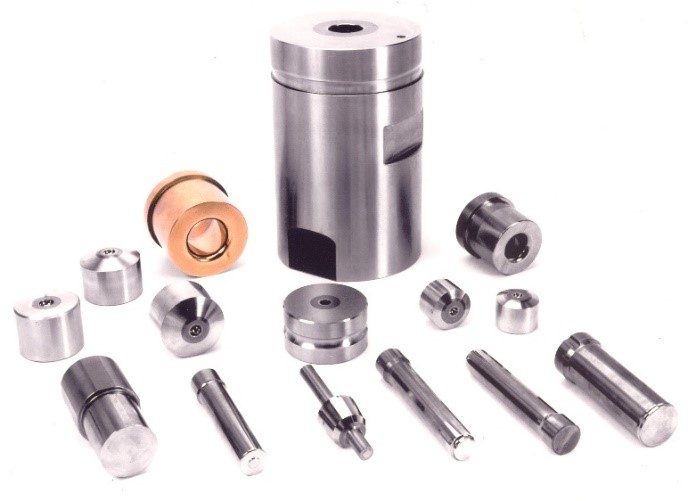
Rising demand for higher productivity requires better tooling material with high wear-resistant properties to withstand high pressure. The ideal option is cemented carbide, which has very high compressive strength, high modulus of elasticity, balanced toughness, and high wear-resistant characteristics.
Cemented carbide is a composite material consisting of tungsten carbide mixed with a cobalt binder matrix and is manufactured through the sintering process. While the material is very hard, it is also brittle in nature as it has a very high-notch sensitivity factor. Unlike steel, the tensile strength of cemented carbide is relatively low, as its hardness and toughness are governed by the percentage of cobalt and grain size of tungsten carbide.
Cold-forming tools such as heading dies made of cemented carbide are designed to sustain high and repeat stress. The toughness and reliability of tungsten carbide can be leveraged to make dies and punches for the mass production of high-volume parts such as screws, bolts, rivets, and other components. Kennametal offers several specialty grades for these types of applications, making it possible for our tooling to perform 6-8 times better than steel tooling and deliver superior part accuracy.
Carbide grades for cold forging application
Kennametal grades GT55, GN50, G45C and GT30 are used in forging applications, depending on the material being forged. For non-ferrous materials like brass, copper etc., harder grades of GT10 and GT20 are used, whereas, for high-tensile materials, Kennametal grades GT20 and GT30 are employed.
Punches are made with BT30 / BT40 grade for forging and GT10 / GT20 grades for sheet metal forming.
Designing punch and die using simulation
Kennametal has knowledge and capability of using software in engineering for analyzing manufacturing processes at various stages through a computer-based simulation. A compression test is also used to determine the flow stress equation to compare the differences between the experimental results and the equation built into the computer simulation software. In addition to planning proper die and punch design and production, the quality of the produced parts would be more stable to promote industrial competitiveness.
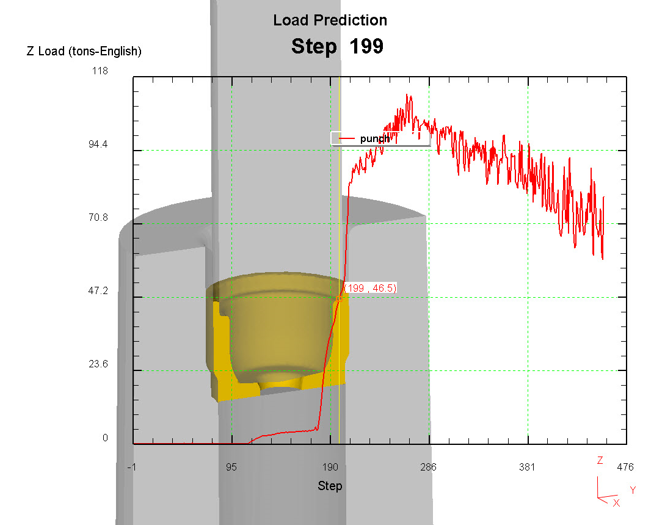
A series of basic operations constitute cold forming in general, based on the principle of shearing, reduction, stressing, extruding, piercing, trimming, and burnishing. There is a tool for each operation with a geometry and material coating specifically designed to meet the final requirement of the finished products.
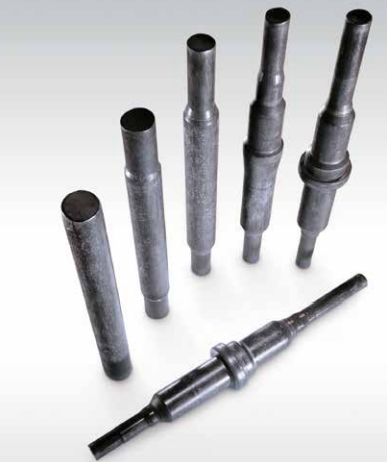
Kennametal specializes in manufacturing the highest quality custom-made tungsten carbide dies and punches for producing desired components and parts through cold forging for high-speed machinery, from billets to finished parts, thus overcoming the need for further machining and ensuring reliable and accurate output.
Product Portfolio – Dies and Punches for Extrusion, Forming, Blanking and Piercing, Heading Dies, Profile Dies
Application – Fasteners, Steering components, Braking components, Transmission components, Engine components, Bearing parts
With our expertise in application, engineering, and manufacturing, we produce precision carbide dies and punches for cold forging applications in line with customers’ requirements.