Researchers from Sandia National Laboratories have developed a 3D-printed superalloy that can generate more electricity and produce less carbon in power plants. The material is made up of 42% aluminum, 25% titanium, 13% niobium, 8% zirconium, 8% molybdenum, and 4% tantalum. It is stronger and lighter than other state-of-the-art materials currently used in gas turbine machinery. The findings could have a significant impact on the energy sector, as well as the aerospace and automotive industries. The superalloy’s strength and low weight properties are believed to be achieved through additive manufacturing technology. The researchers also used advanced computer modeling techniques to predict the material’s performance before it was fabricated.
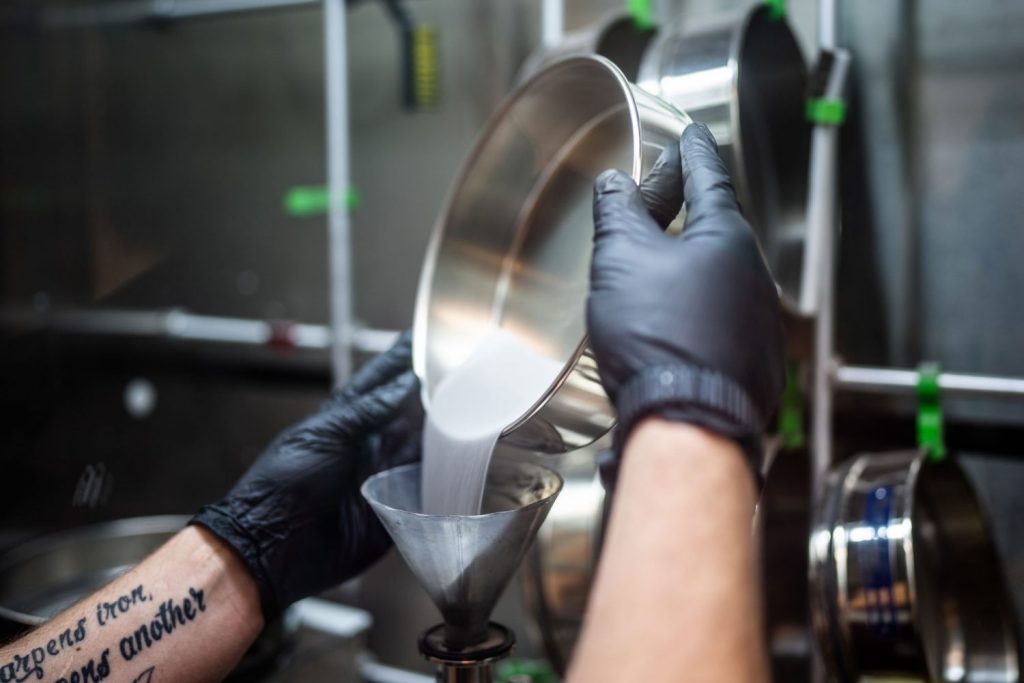
Power plant efficiency is limited by how hot metal turbine parts can get, and if turbines can operate at higher temperatures, more energy can be converted to electricity while reducing the amount of waste heat released to the environment. The superalloy developed by Sandia was stronger than other high-performance alloys, including those currently used in turbine parts, at 800°C and when brought back to room temperature.
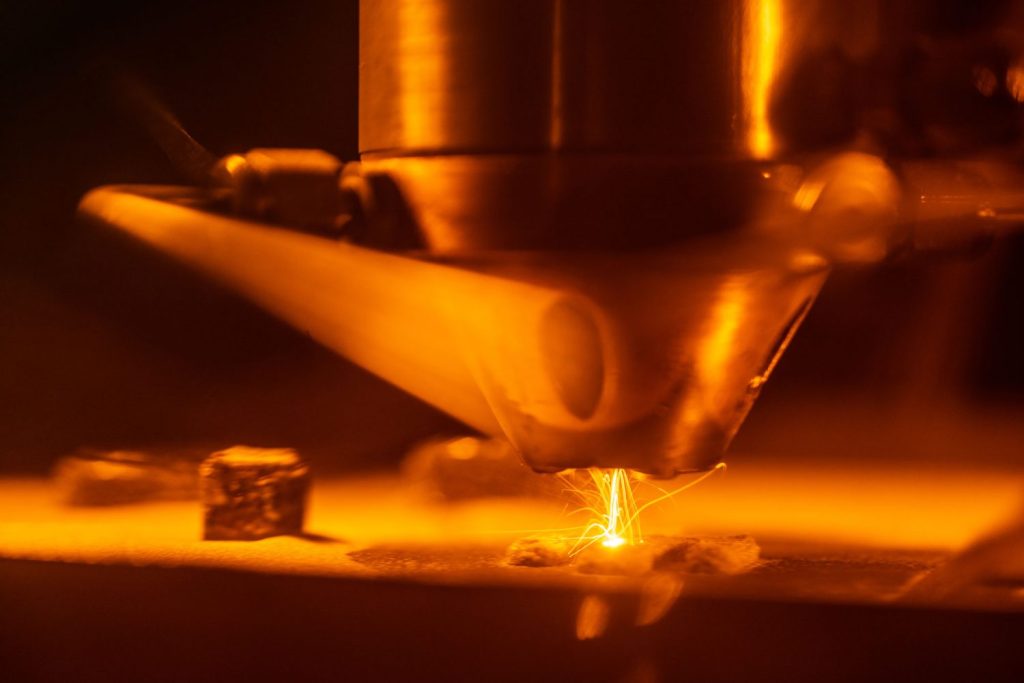
Sandia’s creation represents a fundamental shift in alloy development, with no single metal making up more than half the material. However, scalability and cost are challenges that must be overcome before the superalloy can be produced in large volumes without microscopic cracks. The materials that go into the alloy are also expensive, so it might not be suitable for consumer goods where cost is a primary concern.
Aerospace researchers seek out lightweight materials that remain strong in high heat, and the new alloy could have wide-ranging impacts on energy efficiency in power generation, aerospace, and automotive industries. The research was funded by the US Department of Energy and Sandia’s Laboratory Directed Research and Development program.
Courtesy: Sandia National Laboratories