The industry is in constant search for technology solutions to the challenges it faces. A look into the advanced tools and technology trends in the industry tells you that India is aggressively looking to corner a role for itself as a global manufacturing hub and also aiming big on infrastructure.
Cutting tool industry which derives its demand from across a wide spectrum of sectors is looking forward to seize on the opportunity. Adoptive as they are, Indian manufacturers are looking at challenges at hand in meeting the expected demands and are constantly looking to address them through innovative technologies.
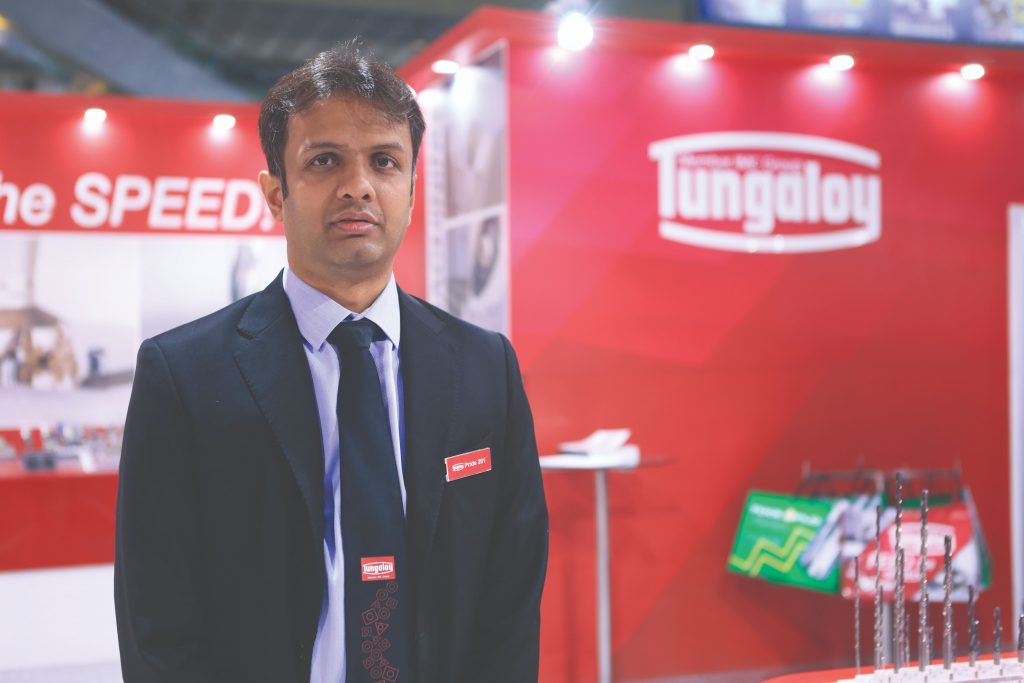
“We have seen a very high level of willingness to try and adopt technologies,” says Jay Shah, Managing Director, Tungaloy India Pvt Ltd.
Demand drivers
Cross-sectoral demand for advanced cutting tool makes the industry well placed to capitalise on opportunities in a growing economy.
“The end markets for drilling and boring tools for instance are highly diverse,” says Prashant Shetty, Director Sales, Metal Cutting, Kennametal India Limited. With demand driven by sectors as diverse as General Engineering, Transportation, Energy and Aerospace market, the demand for advanced cutting tools will continue to rise in the coming years, he feels. More so, because an efficient use of cutting tools impact the overall cost of manufacturing.
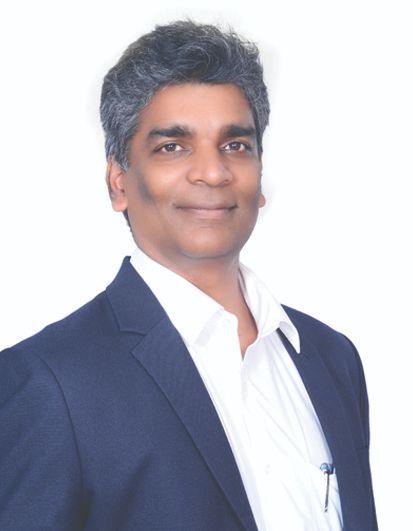
“We are very optimistic about the future and taking steps to capitalise on the potential opportunities in these segments,” he enthuses.
Prashant Sardeshmukh, Managing Director, MMC Hardmetal India Pvt Ltd., includes sectors like railways, defence, die and mould, and medical engineering for the sturdiness of the growth. He particularly draws attention to automotive industry and heavy & light engineering sectors for the “phenomenal growth and technological advancements in the industry.”
Infrastructure is another sector the MMC Hardmetal MD has keen eyes on. “Massive developments in infrastructure and construction activity in the Asia Pacific region are also contributing to growing demand for cutting tools,” he cites.
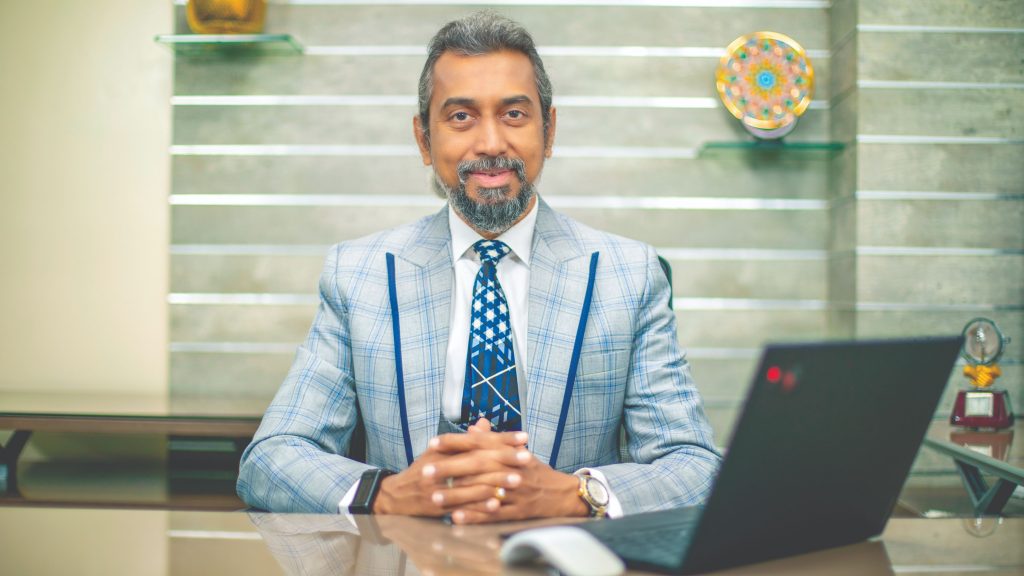
It would be only appropriate in this context to take note of the Indian government’s ambitious Rs 100 lakh crore (USD 1.3 trillion) plan for integrated infrastructure development to assess sectors driving the cutting tool industry.
Cutting tool industry is looking to find a mentionable name for itself in the growth story. But like any other industry at any other time, it has challenges at hand.
Facing challenge
Boring or drilling or deep hole drilling, each applications throws its own challenge in selecting a suitable cutting tool.
The most common among all the cutting tools, a drill, coming in various shapes for varied types of applications, is going through a major shift in terms of technology adoption for a myriad of challenges that it places. Among the most complex machining processes, drilling, deep hole drilling and boring has witnessed introduction of a variety of solutions to challenges they pose.
“Hole making is considered to be one of the most difficult machining operations,” says the MMC MD. At the same time, innovations taking place in the field of hole making play a substantive role in making very sophisticated pieces.
The process of changing drills resulting in higher operation time and the setting of the boring tools resulting in errors and backlashes are everyday challenges on the shopfloor. Chip evacuation, chip jamming, chips getting out of control, and improper evacuation of chips are some of the major challenges that operators face with drilling. Vibration and coolant starvation are some of the other look outs.
Customers getting forced to use centre drills as a pre-drilling operation in long drilling applications is another hurdle that leads to higher operation time, remarks Jay Shah.
Sardeshmukh makes particular mention of the safety hazard as well as damage to the workpiece on account of chip getting out of control, especially while drilling the super alloys or the stainless-steel workpieces.
“Long, stringy chips could get wound up around the drill body leading to safety hazard and damage to the workpiece. On the other hand, short chips generated during drilling of a few varieties of cast iron or some alloy steels, may pose these problems because they do not get evacuated properly leading to breakage of tool and sometime may damage the component or the machine too,” elaborates the Managing Director at MMC Hardmetal.
Finding suitable grades and coatings need also to be addressed.
There is a plethora of challenge searching for solutions and finding answer in technology.
Technology adoption
Sardeshmukh says, “There is a survey that suggests that a lot of Indian manufacturers are adopting advanced manufacturing practices more than the manufacturers from some other advanced countries.”
“Manufacturers today embrace technology much faster than ever before,” presses Ketan Shah, Product Specialist – Hole Making for India at Sandvik Coromant in similar vein.
He illustrates his point by citing the increasing ratio of NPS (New Product Sales) in the market which suggests that the “rate at which customers and manufacturers are embracing change in the technologies is increasing.”
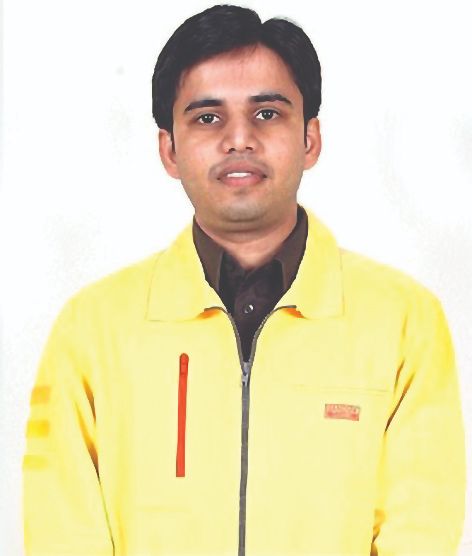
In a competitive market, it is imperative for businesses to create a strong value differentiation to customers. “Adopting emerging trends in cutting tools with innovation, refined manufacturing processes, advanced surface treatments and grades enable manufacturers to create that competitive value differentiation,” remarks Shah to explain the increasing adoption of new technologies.
However, as the industry serves a wide variety of end-customers, the adoption rate of new technologies, of course, varies according to the end markets a manufacturer serves.
Shetty of Kennametal India explains this with examples. Customers producing complex critical parts with tighter tolerances is faster in adopting new technologies as compared to customers producing less critical parts. Similarly, the adoption rate of customers who manufactures components in batches would be different to the ones who do mass production.
Such individual variations apart, “as the manufacturing industry continues to evolve, new technologies will continue to shape the future and cutting tools will lead the charge,” asserts Shetty.
Trending technologies
Finding ways to reduce the cycle time is among the most sought-after solutions with any cutting tool operator.
Shah of Tungaloy talks about how converting solid carbide drills into indexable drills have cut the cycle time drastically. This has increased the cutting speeds and effective feed rates resulting in huge productivity gains, he prides. “Today, we are able to make even a Dia 4 drill in Indexable as launched recently in our ADDFORCE range of products,” he says.
He points out that indexable tools are now being used even in deep drilling. “Our Tri-Deep Drills now start from 12 mm onwards and have been able to transform the machining process in GunDrilling.”
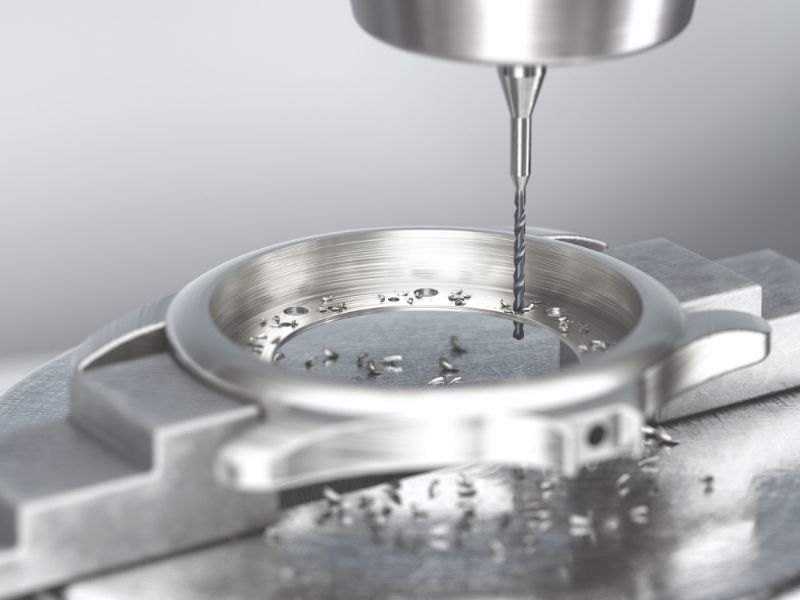
To improve upon chip evacuation, Tungaloy presents splitter design of inserts with which they can break chips in one-third the size.
Chip evacuation is significantly improved with the use of MVE/MVS Series of Drills from MMC Hardmetal, says Sardeshmukh. “It comes with the TRI-Cooling Technology which helps in increase of coolant discharge rates compared to the conventional drills, thereby significantly improving chip evacuation,” he says.
Material removal is another is always a test if it is really to be done striking an ideal balance between tool life, productivity and cost. For solid carbide drilling, Kennametal strikes this balance with Kennametal HP geometry with recent upgrades to HPX and HPR that offer aggressive material removal rates, claims Shetty.
Tungaloy makes use of technology to take care of critical tolerances in boring process with Fine Boring heads which can be adjusted electronically to enable easier changes in size.
Providing centring geometry in the drilling inserts itself is another solution Tungaloy way of facilitating better cycle time to end users.
To take care of the backlash, the eBore comes with an autolocking mechanism that eliminates backlash and errors in setting process.
Selection of coatings and substrates takes some doing too. Among the new trends in the industry is the advancements like nano composite coatings and development of new substrates with advance materials. “The shift in component material sets the tone for the development of cutting tools,” says Prashant Shetty from Kennametal.
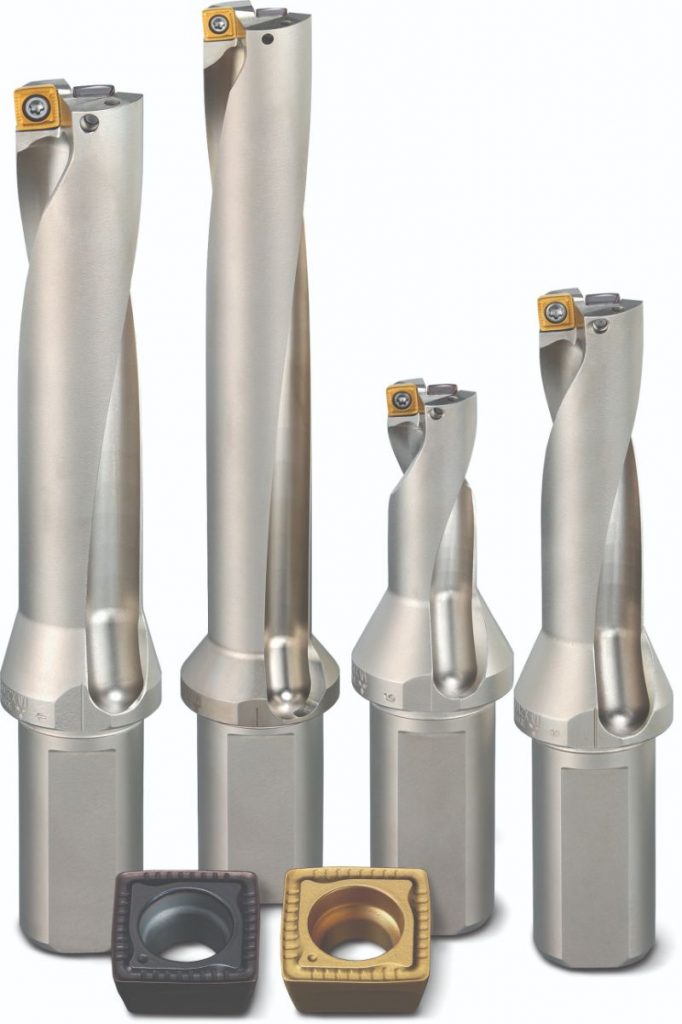
Shah from Sandvik takes care to remind of the new grades and coatings being introduced for their range of drills like the CoroDrill 400, 430, 860-NM and the 865- Sardeshmukh talks of MMC’s DP1120, a PVD coated grade containing fine cemented carbide grains forming ultra-smoothened surface using layer formation techn0logy.
Anti-vibration boring bars or damped boring bars are now available to take care of higher length-to-diameter ratios. “Ultra microfine carbide grades together with coated layers by latest technology makes it possible to machine at higher length-to-diameter ratios,” he updates.
For precision cutting, you have the eBore boring system from Kennametal that provides for smart digital display that communicates to the operator on pre-set values of boring diameters with extraordinary precision, pitches Shetty. “We have recently launched the eBore product lines for finish boring applications that offer a digital interface with extremely precise 1 micron diameter adjustment,” he specifies.
Selection of the most suitable cutting-edge geometry is the key to higher machining efficiency. Therefore, there is constant demand for innovations and upgradation of the drill geometry in terms of the number and position of the drill cutting edges, chip flutes and the angle used.

The R840, among the most popular product ranges from Sandvik Coromant and the largest selling drill in its offering of solid round tools, got upgraded to CoroDrill 860-GM with advanced geometry being its most innovative quality. Elaborating on the upgrade, Shah says, “One of the most innovative qualities of the drill is its advanced geometry, with the double margin adding stability, increased core strength and reinforced corners all of which contribute to process security and finished hole quality.”
He says the flute is highly polished, which helps improve chip evacuation and reduces heat build-up during the drilling process. The CoroDrill 860 with -GM geometry features a new grade, innovative flute design with a multi-layer physical vapour deposition (PVD) coating on the drill tip. “The results are improved drilling capabilities across a range of materials and applications — including general engineering and automotive — and a much greater tool life than its predecessor, the R840.”
Cutting tool industry in India is playing an important part in its march towards Atmanirbhar Bharat. It is in a constant search for innovative technologies to its every day challenges. Eventually, all its search is about improving productivity at the lowest cost.
Global Product Manager at Sandvik Coromant James Thorpe only voices the industry thought when he says, “We are always upgrading our offer and understand that improved productivity along with achieving lower cost per component are two of our customers’ major requirements.”