The cutting tool industry constantly searches for technology solutions to the challenges it faces. To remain competitive, high-end manufacturing companies are looking for accurate, reliable and maintenance-free machine tools offering fast change-over, programming and setup. The machining industry—including capital equipment like lathes, mills, machining centres, forges presses, and injection moulding machines—has been the backbone of manufacturing. It is unlikely that any job shops or manufacturing plants have not invested in this technology.
Automating these machines gives manufacturers clear advantages in terms of utilisation, secondary process, labour resources and productivity. Industrial robot technology could provide an excellent base for machining because it is flexible and affordable. Manufacturers can improve throughput and overall equipment effectiveness by automating the process of loading and unloading machines. Machining robots provide many advantages for users to enhance their operations, improve efficiency and promote increased performance.
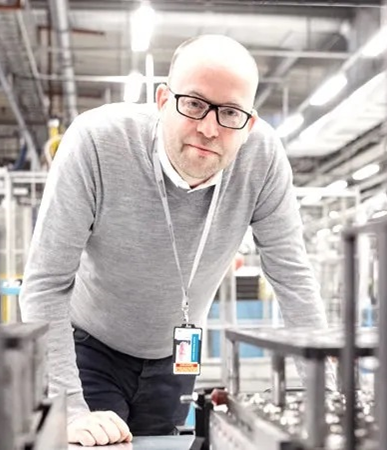
With processes that must deal with more crazy shapes and differing rigidities, an industrial robot can be a great alternative. “Exactly. Part of our digital transformation included the introduction of recall parametric programming. This means programs can automatically adjust and scale themselves based on product requirements. For instance, a drill piece can come in many diameters and lengths. Rather than create drawings for every different possibility, this new programming generates a 3D model of the drill and seamlessly accepts different parameters to render the model. This flexibility made the touchless changeover possible as production changes parameters throughout the day,” shares Lars Matiasson, Manager Global Manufacturing Equipment & Engineering, AB Sandvik Coromant.
Perhaps the most significant advantage of robotic machine cutting tools is their ability to improve worker safety. By automating the cutting process, these machines eliminate the need for workers to operate heavy, dangerous cutting equipment manually. This not only reduces the risk of accidents but also frees up workers to focus on other tasks, increasing overall productivity and efficiency.
Machine tools and robots: the most common applications:
• Handling workpieces: Robots supply the machine tools with workpieces and then remove them following machining.
• Palletizing workpieces: Robots can be used to load standardized containers with a wide range of workpieces down to a batch size of one.
• Linking machines: Robots can be used to link several work steps. Either for loading multiple machines from one source or for feeding workpieces to a machine from various sources.
• Machining workpieces: Robots can take on simple processing steps from the machine tool, thus increasing the productivity of the machine. Moreover, human operators are relieved of machining steps such as brushing and deburring and can therefore focus on more demanding tasks.
• Handling tools: Robots can be used to change tools on the machine directly or with the aid of an internal tool changer. The number of available tools is only limited by the reach of the robot. Linear units can be used to increase the reach of the robot as desired so that one robot can tend multiple machine tools.
In addition to speed and precision, robotic cutting tools are also highly versatile, able to work with a wide range of materials, including metals, plastics, composites, and more. This flexibility means that they can be used for a wide variety of applications, from cutting and shaping sheet metal for car bodies to creating custom moulds for plastic products.
Benefits of robotic machine tending
“Today, a machine operator produces 55 percent more tools compared to 2004, thanks to digitalization and automation. When considering the robotic application at Gimo specifically, the robot inside the Okuma cell reconfigures itself automatically with new collets to accommodate small and large machining orders coming from the factory’s ordering system. This is unique, and means that without much effort, we can tailor orders for one piece to 100 pieces without wasting time or material. Best of all, the robots do it themselves. This is customer value. No one is paying us to reconfigure the robots and the machines manually. In fact, we try not to do anything manually anymore at all,” says Lars Matiasson.
By improving speed, precision, versatility, and safety in the cutting process, they are helping to drive innovation and growth in the manufacturing industry, making it easier than ever to create high-quality products quickly and efficiently. As this technology continues to evolve and become more affordable, we can expect to see even more widespread adoption of these tools in the years to come. Let’s take a closer look at the advantages robotic machinery can provide:
- Consistent high-quality production: a guarantee of consistent quality is one of the most significant benefits. Instead of having one robot that follows one unchanging set of directions per task, modern robotic machinery can fluidly change from one step to the next. Ultimately, robotics improve product quality by reducing defect rates and offering consistently reliable performance.
- Decreased production costs: Robotic machine tending significantly lowers production costs in two ways. Firstly, robots produce goods with greater precision and efficiency, reducing errors and waste and lowering per-unit costs. Secondly, robots work tirelessly and continuously without the same labour costs and overhead as human employees. As robotic machinery advances, the need for lights-on intervals will become increasingly unnecessary.
- Multiple specialised machining operations: Implementing multi-functional robotics optimises valuable floor space and expands service offerings, leading to immediate and long-term financial benefits for companies that invest in this technology.
- Limit hazardous environment exposure: Robotic machinery can operate safely in dangerous environments, reducing liability, healthcare costs, and overall expenses by eliminating manual labour.
A look into the advanced tools and technology trends in the industry tells you that India is aggressively looking to corner a role for itself as a global manufacturing hub and also aiming big on infrastructure.
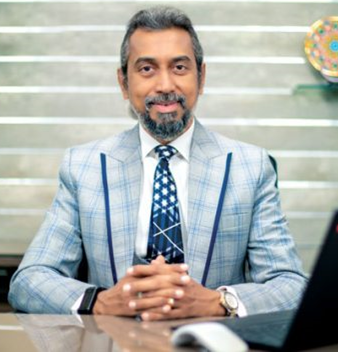
Adoptive as they are, Indian manufacturers are looking at challenges at hand in meeting the expected demands and are constantly looking to address them through innovative technologies. Prashant Sardeshmukh, Managing Director, MMC Hardmetal India Pvt Ltd says, “A lot of Indian manufacturers are adopting advanced manufacturing practices more than the manufacturers from some other advanced countries.”
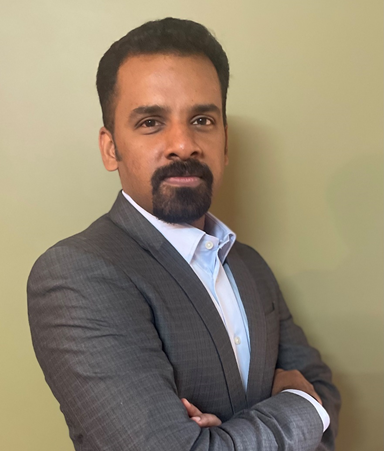
Sougandh K.M., Country Manager of India, Universal Robots said, “India’s automation industry is advancing as it moves towards being a key global manufacturing centre in the upcoming years. The need for robotic automation is growing across all industries, and India, a country with a large workforce, offers more potential for human-robot collaboration. Cobots are ideally suited for automating monotonous and boring jobs, particularly for pick-and-place, deburring, screw driving, and machine tending applications.” Universal Robots recently Robots showcased a variety of industrial grade UR cobots, presenting manufacturers the advantages that cobots offer to the factory floor at IMTEX 2023.”
Siemens SINUMERIK Run MyRobot combines robots with machine tools to provide the right solutions – from simple connections, to the convenient integration for handling tasks, through to the full system integration of the robot kinematics.
Robotic machine-cutting tools are revolutionising the manufacturing industry by offering unprecedented levels of precision and efficiency. These tools by using advanced robotics technology to automate the cutting process not only reduces speed and precision, but are also highly versatile.
Robots and machine tools are a dream team for outstanding productivity. Robotics for the cutting tools industry is a friend or foe? As of now, robots are here to support humans in cutting tool industry and beyond.