In the age of Industry 4.0, the buzzword “predictive maintenance” has become ubiquitous in the manufacturing and industrial sector. PdM 4.0 is the latest version of this technique that leverages artificial intelligence, the Internet of Things (IoT), and other advanced technologies to take maintenance to a new level of accuracy and efficiency. PdM 4.0 uses advanced technologies such as AI, IoT, and data analytics to make maintenance more accurate and efficient. According to Rakesh Prasad from Innover, predictive maintenance is becoming more popular due to the need for organizations to be agile, scalable, sustainable, and resilient.
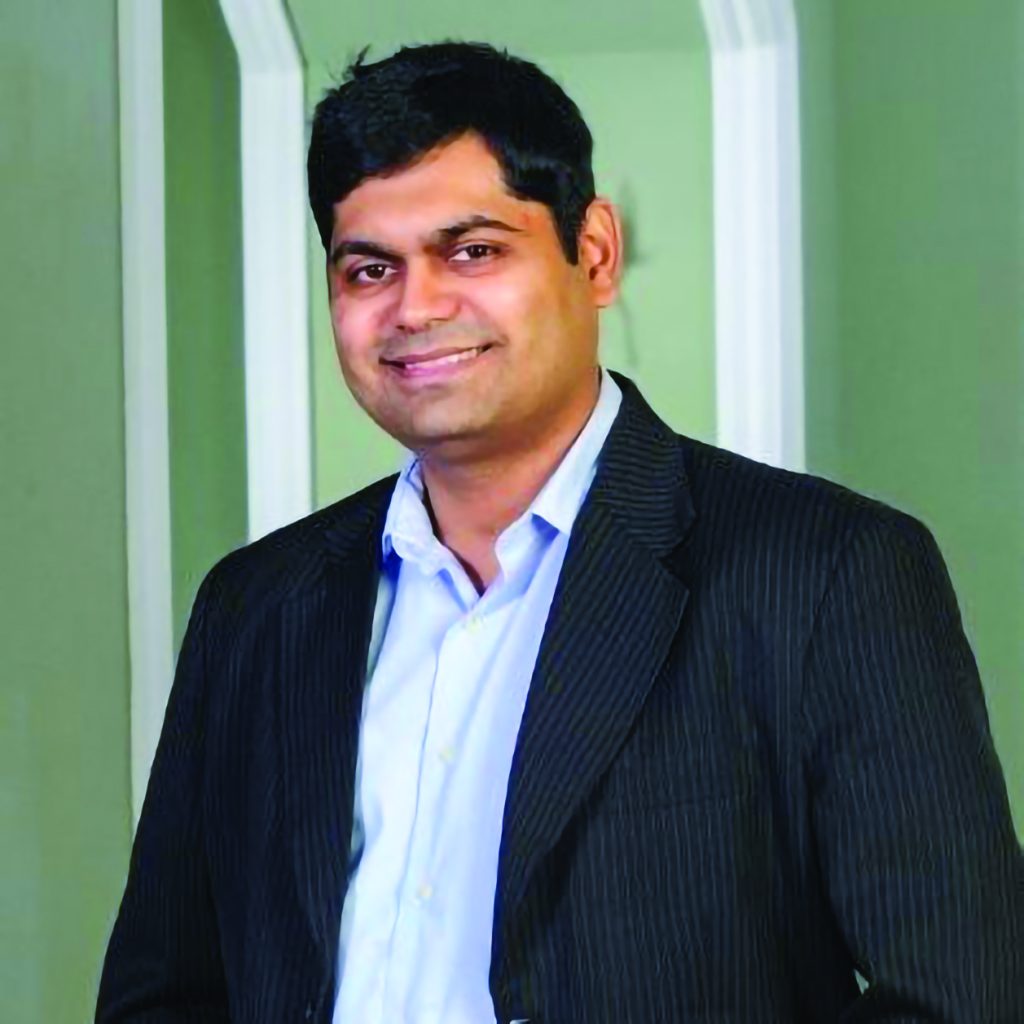
Ramesh Jha from Schneider Electric adds that PdM 4.0 enables timely intervention with minimal downtime, significantly reduces maintenance costs, and enhances operational efficiency. Predictive maintenance 4.0 is a disruptive change from traditional maintenance strategies, which relied on pre-scheduled or reactive maintenance schedules. McKinsey estimates that AI-driven PdM models can reduce annual maintenance costs by 10% and downtime and inspection costs by almost 20%. Addverb’s Bharanidharan S notes that PdM 4.0 aligns with the larger theme of organizations moving from hindsight to foresight for more efficient asset care strategies.
Industry 4.0 & PdM 4.0
Smart factories are equipped with advanced sensors, embedded software, and robotics to collect and analyze data. This allows for better decision-making, increased automation, predictive maintenance, self-optimization of processes, and greater customer responsiveness.
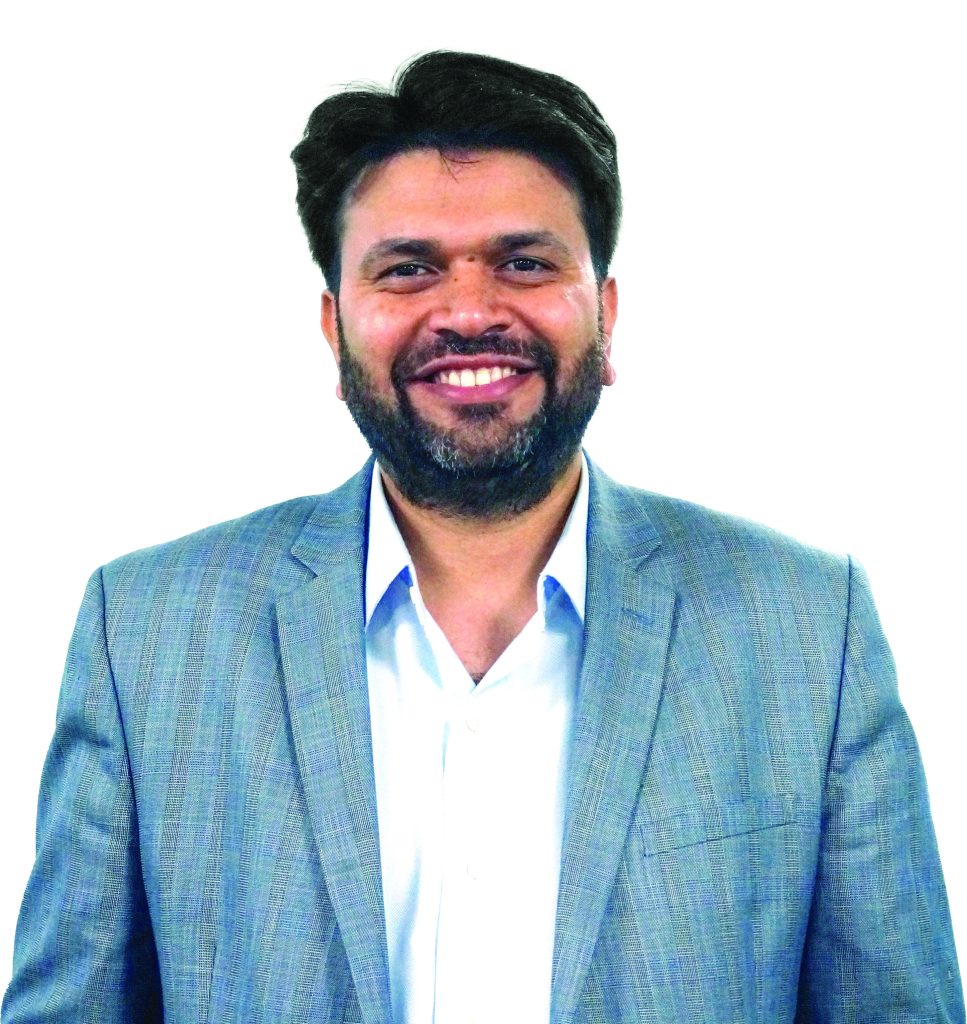
Rakesh observes, “Industry 4.0 has mainly concentrated on Cyber-Physical Systems (CPS) that unify physical and software elements directed by computer-based algorithms. For PdM, IoT sensors are fitted in machines and equipment to monitor their health and surroundings, gathering data on factors such as vibration, temperature, and humidity. This data is then relayed to a central system that employs AI/ML algorithms to examine the data and give insights into the equipment or machinery’s well-being.” Ramesh adds, “Predictive maintenance systems powered by AI can integrate data from multiple sources, making accurate predictions and identifying the root cause of equipment failure. IoT and AI technologies enable predictive maintenance by identifying patterns and making proactive maintenance possible, reducing costs and downtime.”
However, Bharanidharan warns that an effective predictive maintenance approach requires fundamental building blocks such as data collection and analysis, real-time monitoring and triggers, failure analysis, continuous improvement, and capability-building culture.
Measuring the success of their PdM program
To measure the success of predictive maintenance, metrics that were previously used in existing maintenance methods need to be employed to accurately compare results, since this technology hopes to improve upon these metrics. “Existing maintenance KPIs such as Mean time between failures (MTBF), Mean time to repair (MTTR), Mean time before repair (MTBR), and a hoard of such metrics can be used to track the success of predictive maintenance, explains Ramesh. He further details out these KPIs:
- MTBF: Measures the average amount of time that passes between equipment failures. A high MTBF indicates that the predictive maintenance program effectively identifies and addresses potential issues before they become major problems.
- MTTR: Measures the average time to repair equipment after a failure. A low MTTR indicates that the organisation is effectively addressing issues in a timely manner.
- OEE: Measures the overall efficiency and effectiveness of the used equipment. A high OEE indicates that the predictive maintenance program is helping to optimize equipment performance and minimize downtime.
- Equipment Availability: Measures the percentage of time that equipment is available and ready for use. A high availability indicates that the predictive maintenance program is effectively minimizing downtime and maximizing productivity
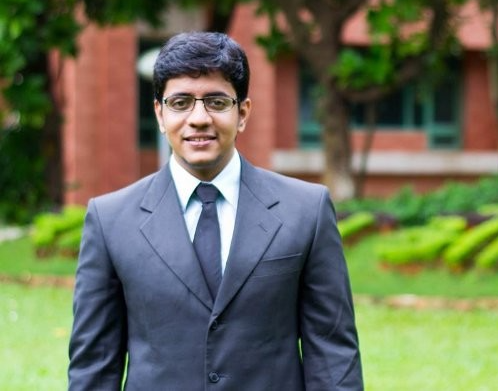
Bharanidharan adds, “While measuring the success of predictive maintenance programs, it is important to always relate to the bigger ‘Why’s – Overall equipment effectiveness improvement, Reduction in costs associated with Maintenance & Equipment – i.e., Labour costs, spare inventory, energy consumption. In addition, specific KPIs are necessary to ensure program continuity and avoid failure.”
The role of data analytics in PdM
At the core of PdM is prognostic techniques, which enable predicting the degradation trend of an in-service system given the real-time measured data.“The importance of effective data management for the success of a predictive maintenance program cannot be stressed enough. Just like Data Science as a concept significantly strengthened by robust data engineering, predictive maintenance gains significant traction when the underlying data management is efficient,” expounds Bharanidharan. Ramesh further clarifies, “Effective predictive maintenance requires more than data collection by smart systems. To ensure accuracy, data must be cleansed and fed into an analytics engine for insights instrumental in predicting maintenance events. Inaccurate data can cause software malfunction, making analytics a crucial technique for accurate predictions.”
Challenges in implementing PdM
Implementing predictive maintenance solutions can be the gateway to many benefits, but setting it up can have its fair share of challenges. Rakesh puts down the points as follows:
Costs & Infrastructure: Collecting and managing large amounts of data from sensors and other sources requires a robust and scalable infrastructure that can handle the data volumes and processing requirements.
Skills & Expertise: The knowledge base for contemporary technologies are scarce and there is a shortage of expert talent that knows the inside-out of how these technologies work and how to implement them.
Change Management: There is friction when adopting new technologies and solutions, and thus, it becomes imperative that such initiatives are driven from top to bottom.
Bharanidharan adds another point: “Efficiency: Having contextual data integrated from multiple sources is complex and needs robust data management and integration systems. Ensuring high standards of data quality is a pertinent hurdle in certain aspects like sensor failure or environmental noises that need to be effectively handled during the data cleansing activity.” Ramesh states that predictive maintenance technology requires time for maturation and industries need to switch to smart systems for maximum benefits, despite incurring large expenses. However, benefits outweigh the upfront costs.
Evolution of PdM in the coming years
PdM has evolved from manual inspections to sensor data and machine learning-based predictions (PdM 2.0) and then to Industrial IoT (PdM 3.0), but with limitations in complexity and speed. Bharanidharan points out three concepts that generate significant excitement when it comes to making predictive maintenance commonplace and more effective:
i) Evolution of Analytics, especially Edge analytics: Edge analytics involves analyzing data closer to the source to quickly detect potential issues and reduce bandwidth and storage requirements. In industries like chemical handling and large-scale operations, real-time analysis is crucial to prevent disasters.
ii) The increasing potential of robotics: Robotic automation can enhance the efficiency and accuracy of predictive maintenance by performing tasks such as equipment inspection and repair on-demand, offering increased reliability and learnability.
iii) Predictive maintenance as a service: Predictive maintenance as a service can leverage economies of scale for data management and ML/AI capabilities, similar to maintenance as a service used by large organizations.
According to Ramesh, predictive maintenance has gained popularity and is expected to evolve rapidly. Advanced analytics tools and cloud-based platforms can provide accurate predictions, while edge computing can improve speed and reduce latency, allowing for quicker detection of equipment failures.
Rakesh is bullish on the future of predictive maintenance. With a forecasted CAGR of 30%, and the predictive analytics market is set to grow from $4.2 billion in 2021 to $15.9 billion by 2026. Prescriptive maintenance and augmented reality may be integrated, creating an intelligent system that can identify and resolve issues, while VR headsets may allow technicians to receive DIY videos and solve problems quickly. Plug-and-play solutions with industry-specific algorithms could become more common, leading to all-in-one identification-to-resolution predictive maintenance systems.
The ethical considerations:
Bharanidharan notes negative outcomes of predictive analytics, such as privacy breaches and inaccurate predictions, impacting large-scale predictive maintenance programs.
i) Data and Employee privacy: Predictive maintenance relies on collecting and storing various data points, which must be done securely and ethically. Organisations should be mindful of sensitive data and provide adequate information to individuals.
ii) Transparency and accountability: Organizations using predictive maintenance must be transparent about their data usage and ensure accountable and auditable decision-making processes, especially if predictions impact individuals. There is a social responsibility to detect failures that could have severe implications.
Ramesh has a word of caution for organisations looking to automate maintenance through the implementation of digital predictive maintenance tools, “Predictive maintenance algorithms can seem like “black boxes”, making it crucial to inform stakeholders about their workings without revealing proprietary knowledge. While improving efficiency and productivity, human decision-making is still critical. Proper employee training is needed for oversight and control over these systems.”