Vishay Intertechnology, one of the world’s largest manufacturers of discrete semiconductors and passive electronic components, has selected Critical Manufacturing’s Manufacturing Execution System (MES) as a new software standard for its business unit Passives. Following the implementation of a pilot plant in Yankton, South Dakota, Vishay plans to roll the new MES out to 30 of its global plants over the next years.
Dr Thomas Amrein, VP Planning & Systems Passive Components / Business Process Owner Planning & Manufacturing at Vishay said, “In our Passive Components business, we have many different and partially outdated legacy systems. This project will remove the risk and the cost associated with maintaining these and create a more efficient, user-friendly solution to take us into the digital future.”
Vishay’s Passive Components plants utilize a combination of legacy and commercial systems, requiring many different tools and packages with individual hardware, software and infrastructure which have been inherited with many different acquisitions over the past decades. Having so many different systems makes it difficult not only to maintain, but also to clearly see how different parts of the plant impact each other.
Dr Amrein continued, “We approached several software vendors but chose Critical Manufacturing because it has a modern, object-oriented approach and offers functional and technical fit, flexibility and an excellent return on investment.”
Francisco Almada Lobo, Critical Manufacturing CEO commented: “Our MES is specifically designed to give the flexibility to meet the demands of sophisticated manufacturing operations such as at Vishay Passive Components. It offers a backbone for Industry 4.0 manufacturing and a data platform to drive efficiency and adaptability to changing business demands.”
The initial Critical Manufacturing MES solution will include material tracking, SAP integration, equipment integration, and provision for manual workplaces. The Connect IoT module enables easy integration of new and legacy equipment and IoT devices and provides a single graphical view of all automation workflows. Engineers can intuitively create and update complex logic with no code required. This forward-looking technology provides a pathway to an increasingly smart production environment, developing at a pace that suits the business needs and strategy.
Dr Amrein further said, “This is an exciting time for our Passive Components business and one that, I believe, will foster greater innovation. The Critical Manufacturing MES will provide us with a platform that not only reduces our exposure to the risk of ageing legacy systems, but also provides us with a way to bring the knowledge, data and best practices of our global operations together to carry out continuous process improvement and harmonization, delivering greater efficiency and enhanced quality to meet our customers’ demands today and well into the more digital future. It will make us stronger than ever and provides us with the flexibility to adapt and change quickly as markets change and new technologies emerge.”
Lobo added, “We have vast experience in the electronics industry, and we are delighted that Vishay selected our solution. We look forward to helping them drive performance and flexibility across their extensive global manufacturing network.”
Vishay Selects Critical Manufacturing MES as its Global Standard for Passives Manufacturing
The initial Critical Manufacturing MES solution will include material tracking, SAP integration, equipment integration, and provision for manual workplaces
SHARE
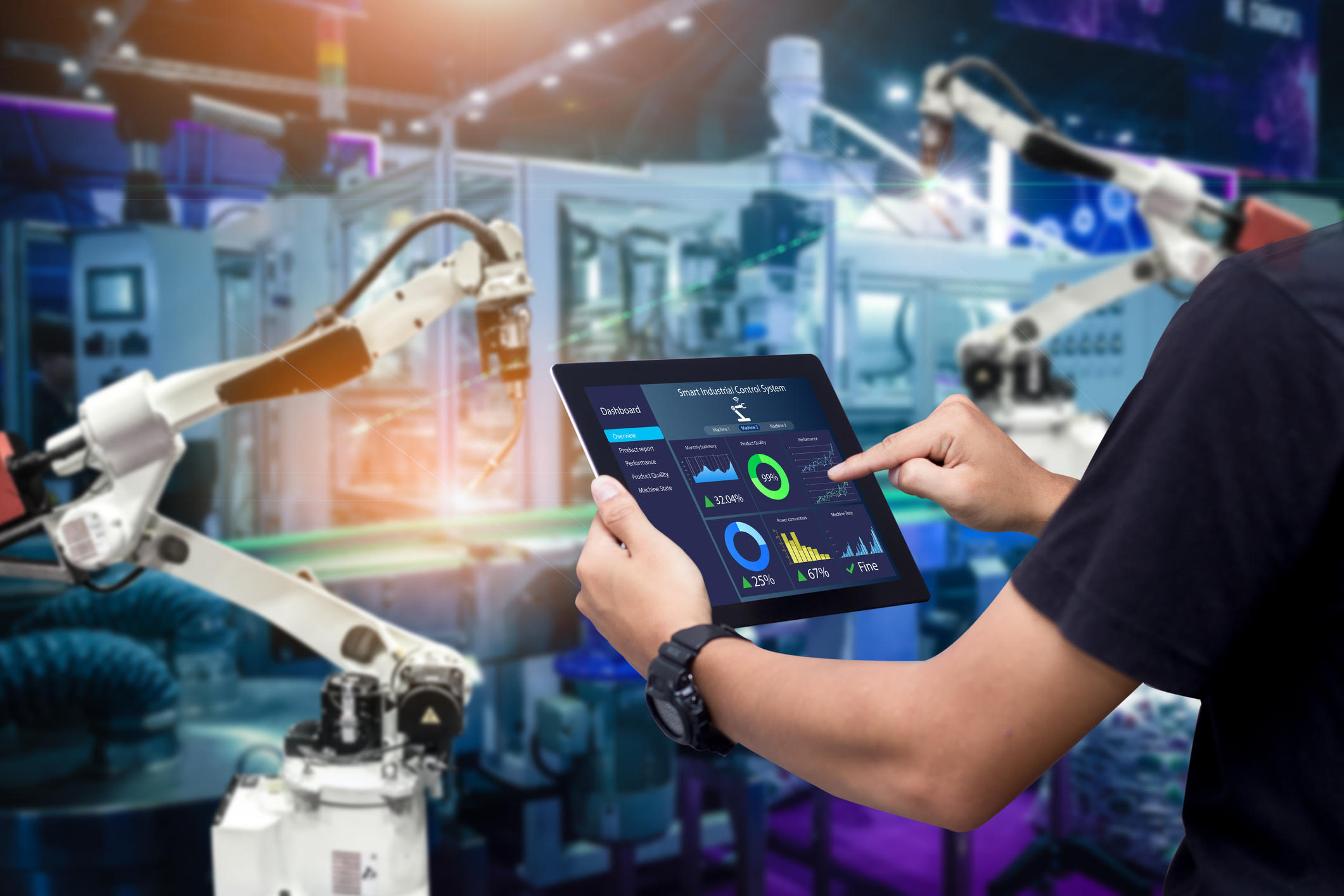